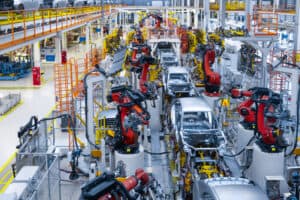
Automotive assembly line virtualization involves the use of digital tools and techniques to model, simulate, optimize, and manage assembly processes before they’re physically implemented.
The ability to virtually design, simulate, test, and commission automated automotive assembly lines is critical to achieving smart manufacturing. Doing so identifies issues virtually, avoiding the costly “design, build, test, break” iteration cycle that delays product launch. The ability to get the manufacturing process design right the first time eliminates many of the painful launch crises that may occur. Identifying assembly issues before they are encountered on a physical line prevents expensive rework and delays.
As such, there is growing interest in production line virtualization. Fortunately, the timing seems right in exploring the topic in that many of the technologies that are needed to virtualize production lines are now routinely available and mature.
What is assembly line virtualization?
Automotive assembly line virtualization involves the use of digital tools and techniques to model, simulate, optimize, and manage assembly processes before they’re physically implemented. The work typically uses digital twins and simulation models that make use of advanced analytics and artificial intelligence.
To that end, before committing to the physical layout of an assembly line, an auto manufacturer can create a digital twin of the line, allowing it to simulate, model, and test various configurations to identify the most efficient setup. Through this modeling, manufacturers can identify potential bottlenecks, inefficiencies, or ergonomic issues for workers.
For example, the digital twin might help a manufacturer see that placing a robotic assembly arm on one side of the line versus the other makes it easier to supply it with raw materials and parts. Or the same model might show that the placement does not give the arm enough room to maneuver without coming dangerously close to a human operator working on the same line.
An additional use of a digital twin model of a production line is to optimize a production’s flow. Again, before anything is built and deployed, an auto manufacturer can virtualize the operation of a workflow through the production line and identify things like the best sequence of tasks for optimal throughput. The digital model can also help a manufacturer fine-tune its processes, optimize movements, reduce wasted time, and ensure that parts and materials are delivered to the assembly line when needed.
Increasingly, sustainability is a growing concern for auto manufacturers. A manufacturer can use the digital representation of its production line to simulate the environmental impact of their processes. They can use that information to adjust and optimize processes to reduce waste and energy usage.
See also: Digital Twins and Other Tech Enable Virtual Commissioning
Additional benefits beyond design
Once a virtualized production line has been mapped out and its workflow optimized, there are other ways to make use of the line’s digital twin to realize additional benefits.
For example, the virtual representation of the line can be used to train workers and develop specific skills they might need to work on a particular line. A worker can walk through operations and understand the correct sequence in which he or she must perform certain tasks.
Or the auto manufacturer can use the simulated model to highlight potential safety issues and proper ways to work to avoid them. For example, the virtual representation of a production line can be used to highlight physical locations along a line where equipment is moving. It can also be used to denote where precautions are needed if hazardous materials are used, equipment reaches high temperatures to the touch, or toxic gases are emitted in the production process.
More benefits once the assembly line is deployed
Once a virtually designed and optimized production line is deployed, there are more ways to use the digital twin.
One recent trend in auto manufacturing (and manufacturing in general) is the need to support highly customized products. Customer requirements change quickly, and they expect manufacturers to quickly meet their changing preferences. Virtualization supports rapid prototyping, where a manufacturer can quickly try out and change production processes to deliver the customized products their customers demand.
Another way to leverage the digital twin is to use IoT sensors on a deployed line and feed data back to the virtualized model for analysis and more simulations. That data and other production process metrics can be used for a number of things. One use would be to combine monitoring of a virtual assembly line in real-time and comparing the performance to the actual physical line. That can provide manufacturers with insights into potential equipment and process problems. Such insights allow a manufacturer to be proactive and anticipate maintenance needs. That, in turn, can help reduce downtime and ensure that the assembly line runs smoothly.
Teaming with a technology partner
Many of the technological elements that must be brought together for such virtualization are not widely used by all auto manufacturers. And even if a manufacturer has the skills, it often does not have the time to pull the elements together into a virtualized solution.
As such, many are looking for a technology partner that brings automotive manufacturing expertise, the needed technology and solutions, and the ability to integrate them together. These are all areas where Siemens can help.
Siemens’ Smart Manufacturing Xcelerator portfolio offers automotive manufacturers the tools to implement intelligent manufacturing. A comprehensive digital twin enables companies to simulate products and manufacturing, providing the flexibility to replicate production anywhere in the world. Closed-loop feedback offers predictive insights that can be used to fine-tune manufacturing and increase uptime to maximize profitability.
Working with Siemens and using digital twin technology to simulate production lines, processes, and even entire plants saves time and avoids unnecessary costs as a line can be thoroughly tested, ensuring changes do not have to be made after installation. It also helps meet the need for speedy changes to meet changing customer preferences and demands.
Additional Resources
Drive production excellence with intelligent manufacturing
The automotive industry is facing unprecedented challenges, with rapid change and intense pressure to meet the demands of climate change, regulations, and consumers. Download Now
Modernize automotive factories with Siemens Smart Manufacturing solutions
Discover how automakers can transform their business with Smart Manufacturing solutions using state-of-the-art hardware and software to modernize production lines. Watch Now
Virtual Manufacturing Development for the Automotive Industry
Companies in the automotive industry are pushing to develop the next generation of autonomous, electric, connected, and shared vehicles. View Now