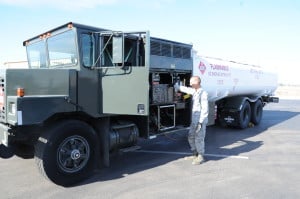
The U.S. Air Force saved $1.5 million in one year through real-time vehicle tracking and condition-based maintenance.
Name of Organization: U.S. Air Force
Industry: Government
Location: Washington, D.C.
Business Opportunity or Challenge Encountered:
For a far-flung organization such as the U.S. Air Force, the need to track vehicles is critical. The service has a fleet of service vehicles — 500 types, which includes a total of 80,000 trucks, Humvees, and automobiles — which are used to maintain bases and transport airmen and aircraft parts.
The challenge for the force was to keep the costs of maintaining these vehicles in line, as well as maintaining a high state of readiness.
How This Business Opportunity or Challenge Was Met:
The Air Force implemented a Condition-Based Maintenance Plus (CBM+) initiative. The CBM+ effort is based on real-time data collection from vehicles to track their condition, as well as analytics to determine when maintenance issues are arising, or where vehicles are located at any time.
The system’s interface provides views into the most complex pieces of vehicles on a day-to-day basis, said Robert Uren, a vehicle equipment specialist for the Air Force. The “leadership view” provides, via color coding, views of the percentage of vehicles that are mission capable and not mission-capable.
“From there, they can drill down by major command, down to specific vehicle category, and down to the individual vehicle level,” said Uren, who spoke at a recent Teradata conference. If a vehicle is undergoing maintenance, the system supplies data on its current status, and the time it will be returned to service.
The system provides data on 68 various attributes that can be selected by users seeking information on vehicle status. An important feature is its ability to project whether it’s more cost-effective to repair vehicles or if they are close to end of life. “Obviously, as you’re working on those vehicles throughout the years, there are costs that go along with it — parts and labor costs,” Uren said.
In addition, the system tracks vehicle use– “how many miles driven, how many hours operated, cost per mile metrics, how many miles driven, our cost over time,” Uren said.
Condition-based maintenance is a key capability, which shifts the control over vehicle management from the operational level to the enterprise, Uren says. “This capability helps facilitate condition-based maintenance for us, capturing all the operational parameters of the vehicle – including excessive speed, fuel consumption and things of that nature,” he says.
Data comes from hardware and sensors installed in vehicles’ dashboards, Uren states. Data streams to the administrative consoles are employed in real-time performance analytics. The data also provides real-time information on measures such as maximum RPMs, engine start times, and idle times.
“We set goals, where if you have 30 parent idle time, we can send a notification to the base managers or to look into that, or talk to the users. Excessive speed is another one,” he said.
In addition, when administrators get notifications that service is required, “we can be proactive and can give our users a call, telling them to bring the vehicle in,” Uren says. “In a worst-case scenario, we’ll get a wrecker,and pick up the vehicle to perform appropriate preventive measures.”
Measurable/Quantifiable and “Soft” Benefits From This Initiative:
The system lets base managers look across specific categories of vehicles and perform what-if analysis, Uren says. “The key metric is health rate,” Uren states. “The higher the health rate the better.”
In addition, the system tracks the average age of vehicles to help determine maintenance needs. These analytics are run by administrators throughout the year, which lists all vehicles recommended for purchase or replacement. “This certainly a case where you feel your job is worthwhile — helping to determine how to spend a large amount of money,” Uren says. “In the first year, we reduced [vehicle] requirements by over a million and a half dollars, and we continue to see results like that over time as well.”
A geospatial feature is now being incorporated that lets Air Force managers locate available assets near bases requiring additional vehicles.
(Source: US Air Force)
Want more? Check out our most-read content:
Frontiers in Artificial Intelligence for the IoT: White Paper
Utilities Need to Get Smarter About Smart Grid
Preventing Downtime With Predictive Analytics
Liked this article? Share it with your colleagues!