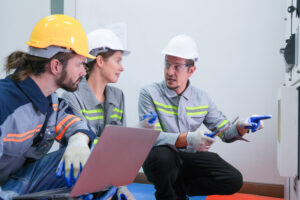
The right-to-repair movement presents an opportunity for technology manufacturers to redefine their relationship with consumers as a preferred service provider.
As the internet of things and edge computing proliferated, companies, especially manufacturers and technology providers, began to shift their business models to draw revenues from service provision, providing software patches, or predictive and preventative maintenance services to customers long after the original sale.
However, companies also added provisions that they be the exclusive providers of these patches or services. Now, pushback from the market, as well as government regulations, are changing those restrictions, potentially opening more competitive services aftermarket.
“Vendors of software-infused goods have increasingly used digital control over their products to capture additional post-sales value in recent years,” according to Jan Recker and Gerald C. Kane, writing in MIT Sloan Management Review. Often, companies will “require subscriptions to keep appliances operable or when they remotely limit owners’ ability to fix products when they break.”
Though they have paid for the goods, customers “do not always enjoy what most consider to be full rights of ownership,” Recker and Kane write. “And they are becoming increasingly unhappy about it.”
The result will be greater competition in the services aftermarket, with implications for internet-of-things approaches to support. “Vendors of software-infused goods have increasingly used digital control over their products to capture additional post-sales value in recent years,” Recker and Kane write. This includes requiring subscriptions “to keep appliances operable or when they remotely limit owners’ ability to fix products when they break.”
A prime example is Deere & Co.’s post-sale support of its tractors with sensors and software. However, because it restricts third-party access and maintenance of its equipment, the company faces lawsuits and actions by state attorneys general. The push is on to allow customers “to make modifications, customizations, or repairs to the products themselves, or via an independent repair shop, without negative consequences,” the co-authors observe. “Right-to-repair laws have passed in California, Colorado, Maine, Massachusetts, Minnesota, New York, and Oregon, and bills are currently active in 30 state legislatures. The European Union adopted a new set of right-to-repair rules in 2024.”
The right-to-repair movement “presents an opportunity for technology manufacturers to redefine their relationship with consumers as a preferred service provider.”
See also: How Will Prediction Models Impact the Future of Vehicle Maintenance?
Starting down the right-to-repair path
Recker and Kane suggest three key strategies for competing in a right-to-repair environment, while still offering state-of-the-art, real-time technology connectivity.
Develop a service-centric business model. “Companies that have collected service revenue by locking customers into rigid service or maintenance schemes need to reimagine service as a competitive business, because it will become only more so as regulations knock down barriers to entry,” they write. “That means putting customer solutions, not product sales or control, at the center of the business.”
Rethink product design with repair in mind. “Product manufacturers have often taken the proprietary route to maintain control of the product experience, but they will need to cede some control in order to empower product owners to exercise repair rights.”
Build analytics into products to gain an edge in services. “With analytics directly built into the products to monitor product performance, manufacturers can diagnose maintenance issues before a customer suffers a product failure. Product-in-use analytics also provide manufacturers with crucial insight into patterns of user behavior and allow them to monitor product health trends across the installed base. That data can inform predictions about future demand for maintenance, repair, or product replacement and help manufacturers organize service offerings to meet current needs.”