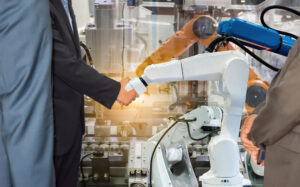
The true value of intelligent manufacturing technologies like AI, digital twins, IoT, and more is unlocked when people are empowered to oversee, adapt, and optimize their use.
The real power of intelligent manufacturing lies not in the mere presence of advanced technologies but in how effectively these technologies work together. We’re talking about AI, machine learning, digital twins, edge computing, IoT, and blockchain. Together, they create a seamless, interconnected ecosystem that helps solve some of the biggest inefficiencies of past manufacturing. Manufacturers can move beyond isolated improvements and achieve a level of operational excellence that wouldn’t be possible with individual technologies alone:
- AI and machine learning enable machines to learn from data and make autonomous decisions.
- Digital twins provide real-time simulation and feedback to optimize processes and assets across their lifecycles.
- Edge computing brings critical data processing closer to where it is needed, supporting ultra-low latency decision-making on the factory floor.
- IoT ties all these technologies together, creating a digital thread that ensures data flows continuously and accurately across all stages of production.
- Blockchain adds a layer of trust and transparency, securing data integrity and streamlining compliance.
However, these technological synergies are not self-managing; their effectiveness hinges on human oversight and strategic coordination. People must still interpret data, adjust workflows, and ensure that insights translate into actionable strategies that drive growth. The true value of intelligent manufacturing emerges when human expertise and technological power are combined, fostering a culture of continuous improvement and innovation.
People Are the Key
The true value of intelligent manufacturing emerges when human expertise and technological power are combined, fostering a culture of continuous improvement and innovation.
The Role of Cross-Functional Teams and Integrated Workflows
It’s not just about having data scientists, engineers, IT specialists, and operations managers in the same room. They must work together seamlessly, with shared business-oriented goals and integrated workflows.
- Creating a Culture of Continuous Improvement and Collaboration: Shifting mindsets from protecting data within silos to sharing insights across teams to drive better decision-making. For example, production teams must collaborate with IT and data science teams to ensure that data collected from the shop floor is accurately processed and analyzed.
- Integrated Workflows and Real-Time Feedback Loops: Leveraging integrated workflows enabled by digital platforms that connect disparate systems and processes for real-time feedback loops. Information moves from one stage of production to inform and optimize the next. For instance, data from IoT sensors on the production line can trigger immediate adjustments in supply chain orders or maintenance schedules, aligning all departments towards common goals and increasing overall efficiency.
Human-Machine Collaboration: Redefining Workforce Roles
In an intelligent manufacturing environment, human workers and machines work side-by-side, complementing the other’s strengths. Rather than replacing human workers, intelligent technologies augment their capabilities, allowing them to focus on what requires creativity, critical thinking, and problem-solving.
- Empowering Workers with Augmented Intelligence: Augmented intelligence tools, such as AI-driven analytics dashboards or wearable devices, provide workers with real-time insights that enhance their decision-making and operational efficiency. For example, machine operators can use augmented reality (AR) glasses to receive step-by-step guidance on complex assembly tasks, reducing errors and speeding up production.
- Redefining Roles and Upskilling the Workforce: As machines take over routine and repetitive tasks, the roles of human workers evolve. Manufacturers must invest in upskilling and reskilling programs to support employees as they learn to work alongside advanced technologies. This includes training on data analysis, machine learning, and IoT systems, as well as fostering a mindset of continuous learning and adaptation.
Aligning Processes with Technology to Achieve Business Goals
Intelligent manufacturing requires rethinking existing processes and business goals to ensure they are compatible with and enhanced by new technologies. This also requires stakeholder buy-in.
- Process Reengineering for Agility and Flexibility: Intelligent manufacturing thrives on flexibility and agility. This means redesigning processes to be more modular, adaptive, and capable of rapid reconfiguration in response to changing market conditions, customer demands, or supply chain disruptions. For example, adopting a modular production process allows manufacturers to quickly shift from one product to another without significant downtime or retooling.
- Embedding Continuous Improvement into Daily Operations: Intelligent manufacturing is a journey, not a destination. It requires a continuous improvement approach where processes are constantly evaluated and optimized based on real-time data and feedback. Lean manufacturing principles, combined with data-driven insights, enable companies to identify inefficiencies, reduce waste, and improve overall productivity continuously.
Driving Innovation Through Integrated Ecosystems
Creating synergies across people, processes, and technology turns manufacturers into dynamic innovation hubs capable of quickly responding to market opportunities and challenges.
- Fostering an Ecosystem of Partners and Stakeholders: To achieve true intelligence, manufacturers must collaborate not only internally but also with external partners, suppliers, and customers. This ecosystem approach allows for co-innovation, where insights and expertise from all stakeholders contribute to developing new products, services, and business models.
- Leveraging Open Platforms and Standards for Innovation: Open platforms and standards facilitate interoperability between different technologies, tools, and systems, enabling manufacturers to innovate faster and more efficiently. For example, adopting open IoT standards can make integrating new devices and sensors into existing systems easier, accelerating the deployment of intelligent manufacturing solutions.
Achieving Excellence Through Intelligent Manufacturing
Intelligent manufacturing represents a new era where technology and human expertise converge to create dynamic, resilient, and growth-oriented operations. Integrating AI, machine learning, digital twins, edge computing, IoT, and blockchain drives unprecedented efficiency, agility, and innovation. Yet, the true value of these technologies is unlocked when people are empowered to oversee, adapt, and optimize their use.
By fostering a culture of collaboration, embracing continuous improvement, and aligning technological capabilities with strategic goals, manufacturers can transform their operations from reactive to proactive, from cost centers to strategic assets. The journey to intelligent manufacturing may be complex, but the rewards — from enhanced operational performance to sustainable growth — are worth the effort.