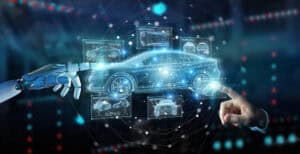
By integrating Autonomous Mobile Robots (AMRs) and Automated Guided Vehicles (AGVs) into their operations, automakers can reduce costs, increase agility, and future-proof their factories.
The automotive industry has long been at the forefront of automation, using industrial robots for decades to assemble, weld, paint, and inspect vehicles with high precision. However, the next frontier of manufacturing efficiency isn’t just about robots working in fixed positions—it’s about robots that move intelligently and autonomously within the factory floor.
In particular, Autonomous Mobile Robots (AMRs) and Automated Guided Vehicles (AGVs) are poised to revolutionize material handling, logistics, and workflow efficiency in modern auto plants. These mobile robotic solutions are an upgrade and a paradigm shift in factory automation.
What Are AMRs and AGVs?
Automated Guided Vehicles (AGVs) are mobile robots designed to transport materials within a manufacturing facility, warehouse, or distribution center. They operate by following predefined paths, such as magnetic strips, embedded wires, or laser guidance systems. AGVs have been in use for decades, primarily for material transport, and they excel in structured environments where the layout does not frequently change.
Autonomous Mobile Robots (AMRs) take mobility to the next level. Unlike AGVs, AMRs are equipped with advanced sensors, cameras, and AI-driven navigation systems that allow them to move freely and dynamically within a facility. They don’t require predefined paths and can adapt to real-time obstacles, re-routing themselves intelligently without human intervention. That makes them far more flexible in environments that require constant change and optimization.
They differ from traditional manufacturing robots in a number of ways. For instance, traditional industrial robots, such as robotic arms used in assembly lines, are stationary. They perform highly specialized and repetitive tasks with extreme precision but lack mobility. They are typically bolted in place and require extensive programming and setup to integrate into production lines.
In contrast, AMRs and AGVs introduce mobility and autonomous decision-making to manufacturing operations. While traditional robots handle tasks like welding and assembly, AMRs and AGVs focus on material transport, inventory movement, and factory logistics—crucial elements that can significantly impact production efficiency.
Mobile and Autonomous Robots Bring Multiple Benefits
AGVs and AMRs provide significant advantages for auto manufacturers looking to streamline operations, reduce costs, and increase flexibility. Some of the key benefits include:
Increased Efficiency and Productivity: Manufacturing plants rely on smooth logistics to maintain production efficiency. AMRs and AGVs ensure that materials, components, and tools are delivered exactly when and where they are needed, minimizing downtime and production bottlenecks.
Reduced Labor Costs and Workforce Optimization: Labor shortages and rising wages drive manufacturers to seek automation solutions that reduce dependence on human labor for repetitive tasks. AMRs and AGVs handle material transport, allowing human workers to focus on higher-value tasks that require creativity and problem-solving.
Enhanced Safety: Automated vehicles reduce the risk of workplace accidents caused by human error, such as forklift collisions or improper material handling. AMRs, in particular, are designed with advanced obstacle detection and avoidance systems, ensuring a safer factory environment.
Scalability and Flexibility: AMRs are particularly valuable for their adaptability. As production needs change, they can be reprogrammed or re-routed without requiring major infrastructure changes. That is crucial for auto manufacturers dealing with customization trends, electric vehicle production shifts, or fluctuating supply chain conditions.
Improved Inventory and Logistics Management: AMRs and AGVs integrate with warehouse management systems (WMS) and enterprise resource planning (ERP) systems, ensuring real-time tracking of parts and materials. This level of visibility helps prevent stockouts, delays, and inefficiencies in supply chain operations.
See also: The Increasing Role of Cobots in Automotive Smart Manufacturing
A Look Under the Hood of the Newest Auto Manufacturing Robots
There are a number of technologies that empower these new robots with autonomy and automation. Specifically, to operate effectively in an automotive manufacturing environment, AMRs and AGVs rely on a combination of advanced technologies.
Both types of robots need navigation and mapping technologies. To follow fixed paths, AGVs typically use magnetic strips, QR codes, or laser guidance. AMRs use LiDAR, cameras, and AI-driven SLAM (Simultaneous Localization and Mapping) to navigate dynamically.
AGVs and AMRs typically connect to IIoT platforms, integrating with factory automation systems to enable data sharing, predictive maintenance, and remote monitoring. To do that, they require Wi-Fi, 5G, or other wireless connectivity to communicate with central control systems and other elements on a factory floor.
Additionally, AMRs often leverage AI to process data from sensors and cameras, allowing them to adapt to changing environments, predict potential obstacles, and optimize their routes in real time.
See also: Making Smart Manufacturing Smarter with AI
Implementation Considerations for Auto Manufacturers
For companies looking to adopt AMRs and AGVs, there are a number of key factors to consider.
One issue is the costs of moving to and using the new generation of robots. While AMRs and AGVs reduce long-term costs, upfront investment in hardware, software, and training must be taken into account.
Another aspect of their use relates to the factory layout. AGVs require fixed infrastructure changes, while AMRs can adapt dynamically, making them more suitable for rapidly evolving production lines.
The robots will need to integrate with existing automation systems. Ensuring that AMRs and AGVs can communicate with existing robotic arms, conveyors, and enterprise software is crucial for seamless operations.
A Final Word on AMR and AGV Robots in Auto Manufacturing
As the automotive industry continues to evolve—with increasing adoption of electric vehicles (EVs), autonomous cars, and customized production models—the need for flexible, intelligent, and scalable automation will only grow.
AMRs and AGVs will play an even greater role in smart factories, seamlessly integrating with AI-driven quality control, predictive maintenance, and real-time supply chain management. Companies that embrace these mobile robotic solutions now will be better positioned to lead in the next generation of auto manufacturing.
By integrating AMRs and AGVs into their operations, automakers can reduce costs, increase agility, and future-proof their factories in an increasingly competitive landscape. The time to act is now.