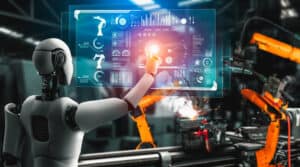
The automotive industry’s embrace of smart factory modernization will revolutionize production processes (and, in many cases, already has), enabling real-time monitoring, predictive maintenance, and optimized workflows.
Shifting to a smart manufacturing model in the automotive industry has paved the way for more efficiency and flexibility. Smart factory modernization is the process of integrating advanced technologies and data-driven solutions into traditional manufacturing setups, which allows manufacturers to optimize their production processes, reduce costs, and improve overall productivity. Here are some key strategies for smart factory modernization and real-life use cases.
Internet of Things Integrations
Implementing IoT devices and sensors throughout the factory floor enables real-time monitoring and data collection. This data can be used for predictive maintenance, tracking production progress, and identifying bottlenecks to optimize the workflow. These sensors have become so ubiquitous that it’s driven greater cloud adoption in an effort to manage the sheer volume of data collected and opened up new SaaS models to handle processing.
Luxury car company BMW has pioneered IoT and Industry 4.0 technologies in its customer-facing applications (such as in-vehicle features) and production facilities. They implemented IoT devices and sensors to monitor equipment performance, track inventory, and optimize logistics within their factories. It even launched the Open Manufacturing Platform to provide a framework with open APIs and model industrial solutions such as IoT.
Big Data Analytics
Analyzing the data generated by IoT devices and other sources helps in making data-driven decisions. By understanding patterns and trends, manufacturers can optimize processes, predict maintenance needs, and improve quality control. But big data analytics isn’t just any process; manufacturers must be able to gather, store, and process extreme data volumes quickly and effectively. Once they do, the patterns that emerge provide priceless input in major decisions and can even help predict future outcomes.
Tesla is an excellent example of this. The company gathers an astonishing amount of data from its connected vehicles and leverages this insight to catch defects early, provide features customers want, and streamline the design process. Additionally, big data analytics is helping Tesla inch closer to the ultimate automotive goal—the first truly autonomous vehicle.
See also: Researchers Amplify Impact of Generative AI in Auto Design
Artificial Intelligence (AI) and Machine Learning (ML)
AI and ML technologies can be employed to optimize production schedules, predict machine failures, and automate quality control processes. These technologies help in making smart and adaptive decisions based on real-time data and, often, data volumes that would be challenging for humans to process. Some car manufacturers are integrating AI/ML into the operational workflow of their factories to assist workers and managers.
Audi, for example, is using AI in production in several capacities. First, AI monitors body construction at the Neckarsulm site to ensure quality spot welds. Human workers no longer have to check every single weld and can focus only on problems. At its Ingolstadt press shop, AI is checking the quality of pressed parts to monitor for cracking, yet another area where human workers no longer take on the bulk of quality control.
Robotics and Automation
Integrating robotics and automation in the production process can enhance efficiency and flexibility. Robots can take over repetitive tasks, allowing human workers to focus on more complex and creative aspects of manufacturing. And according to the International Federation of Robotics, the automotive industry employs the most robots of any other sector—over one million work in the car industry worldwide.
Robots are handling everything from stepping in to handle manufacturing tasks that previously required human intervention, managing quality control, and establishing higher quality and safety standards.
Cloud Computing
The cloud is another advancement like AI/ML that allows manufacturers to scale to meet processing needs from big data. Leveraging cloud-based solutions will enable manufacturers to access and analyze data from anywhere, promoting collaboration between different teams and facilities. This is good news as more car companies operate across a distributed supply chain and national borders.
With many configurations available for cloud computing, car manufacturers can more easily disseminate information between facilities and double-check for consistency. They can also more easily manage compliance requirements in different locations by leveraging multi-cloud architectures. This “web of processing” enables companies to deploy new technologies like AI/ML or digital twins and readily operate with the flexibility modern manufacturing requires.
Digital Twins
And speaking of digital twins, this technology minimizes risks and enables better planning and optimization. Digital twins allow automotive manufacturers to simulate any number of things—the design and assembly of vehicles, production process, and defect inspections—and optimize them before anything takes place in the real world. They can even be extended to represent the entire supply chain, allowing manufacturers to simulate best and worst-case scenarios to improve logistics and reduce lead times, even in times of disruption.
BMW and General Motors are already working with major tech companies to design and deploy omniverse platforms that seamlessly connect different 3D virtual worlds. French car company Renault is working on its own version of a metaverse that includes twins for everything from the car to the supply chain.
Additive Manufacturing (3D Printing)
Adopting 3D printing technology can reduce production time, decrease material waste, and enable on-demand production of customized parts. This capability helps streamline operations when customers demand customization options more frequently while expecting faster delivery times. It provides a sustainability edge because 3D printing wastes fewer materials than traditional manufacturing and enables small-batch production for prototypes, special editions, and replacement parts.
Ford Automotive has poured millions into its new assembly lines, incorporating 3D printing, among other solutions, to improve production efficiency. And as of last year, these additive printers can work autonomously, adding a new layer of efficiency.
See also: Smart Manufacturing: Melding Digital and Physical Worlds
Building the factories of tomorrow
The automotive industry’s embrace of smart factory modernization and additive manufacturing will revolutionize production processes (and, in many cases, already has), enabling real-time monitoring, predictive maintenance, and optimized workflows. Integrating new technologies like cloud computing, digital twins, and AI/ML, car manufacturers are making strides toward a more sustainable manufacturing process. And as the industry continues to evolve and embrace cutting-edge technologies, the future holds the promise of even more exciting and groundbreaking developments in smart automotive manufacturing.