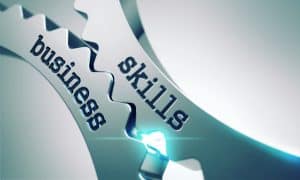
Business leaders need to invest more in creating a future-ready workforce to overcome skills gaps that can impede progress towards a real-time enterprise.
Gaining competitive advantage with the Internet of Things, artificial intelligence, and all the other state-of-the art intelligent technologies, doesn’t come from relying on systems and machines. It’s going to take a well-trained, highly collaborative workforce for technology to fall into place. Otherwise, you are only dropping expensive technology on top of a moribund organization.
See also: FRESH DATA: 96% of AI/ML Projects Have Training Problems
That’s the word from a new study released by Intel, focusing in the promise and challenges of Industry 4.0, which aims to digitally connect all corners of the manufacturing sector. While the technology is awe-inspiring, it won’t deliver any impressive results until a growing skills gap is addressed.
Business leaders need to invest more in creating a “future-ready workforce,” urge the study’s authors, Dr. Faith McCreary and Dr. Irene Petrick, both with Intel. “With the increasing proliferation of data, connectivity and processing power at the edge, the industrial IoT is becoming more accessible. However, successful adoption remains out of reach for many: two of three companies piloting digital manufacturing solutions fail to move into large-scale roll-outs,” they point out.
Of the leading challenges faced in moving to Industry 4.0, the growing skills gap leads, cited as an issue by 36%. Other challenges mentioned include data privacy and interoperability.
The study finds that while there is a big appetite for digital transformation – 83% of companies plan to make investments in smart factory technologies – the most important skills and characteristics cited for that transformation are not ones that are typically emphasized by most industry job training programs.
Future skills cited by respondents point to the need to go beyond the basics of programming to embrace a deep understanding of digital tools, from data collection to analytics and real-time feedback directly to the operating environment. The top five future skills required to support digital transformation in manufacturing include the following:
- Deep understanding of modern programming or software engineering techniques
- “Digital dexterity, or the ability to leverage existing and emerging technologies for practical business outcomes
- Data science
- Connectivity
- Cybersecurity
Another consideration in addressing the skills gap is the way people will be trained to interact with machines and systems. Employees’ abilities to be productive within a highly connected and intelligent environment will stem from their ability to work collaboratively with “digital” workers to accomplish tasks, according to J. P. Gownder, an analyst with Forrester, who shared the results of his research into the new workforce at an Automation Anywhere conference in New York.
Automation doesn’t mean replacing someone. “A lot of times what happens is as you actually get into the process, you find human employees a lot more valuable than thought,” Gownder says. “They can be upskilled.” Twenty-nine percent of executives in a Forrester survey are thinking that intelligent automation will be used to “free up personnel for higher-level tasks — achieving higher levels of quality, or reinventing your business model,” he points out.
That’s because automation is taking on a plethora of tasks — from call centers to services, but not entire job roles. “When you think about an employee, you need to think not only about the human but what are the digital workers that are going to help that human do their jobs? What is the intelligence and software that’s going to make that most effective,” said Gownder. “We’re increasingly disaggregating jobs into a series of tasks. And we’re saying, where are the skills to attend to those tasks? That could be from the gig economy. That could be from outside bringing in outside employees. But increasingly it’s going to be bots that have specialized skills that can take on tasks.”
In Forrester’s survey, “80 percent were at least interested in robotic process automation and intelligent automation,” he said. However, human workers need not fear for their employment prospects — human and digital workers will increasingly be working side by side, opening up new avenues of innovation.