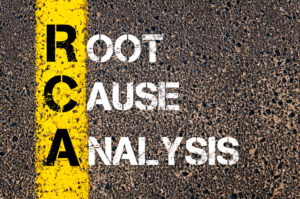
By leveraging AI and comprehensive data management, organizations can enhance the efficiency and effectiveness of root cause analysis in industrial operations, leading to improved safety, reliability, and productivity.
Industrial organizations typically approach root cause analysis (RCA) using structured methodologies designed to identify the underlying cause of equipment or process failures—not just the symptoms. Increasingly, organizations are turning to artificial intelligence (AI) to complement traditional methods and take RCA to new levels.
Why the change? For years, the goal of RCA has been to quickly solve problems and implement long-term corrective actions that prevent problems from reoccurring. RCA strategies would often begin with data collection from various sources, including sensor data, maintenance records, operator logs, and control systems. Teams would then use this information to construct a timeline of events and narrow down the sequence that led to the failure.
Common tools and frameworks used in RCA include the “5 Whys” technique, Fishbone (Ishikawa) diagrams, and Failure Modes and Effects Analysis (FMEA). In complex industrial environments, cross-functional teams—comprising operations, maintenance, engineering, and safety personnel—collaborate to analyze the failure from multiple perspectives.
Limitations of Traditional RCA
Traditional RCA can be time-consuming and limited by human bias or incomplete data. It often relies heavily on expert knowledge and manual investigation. As a result, some root causes may go undetected or be misattributed, especially in systems with interdependent variables or delayed failure effects. To that point, traditional RCA methods in industrial operations have several limitations that can hinder their effectiveness despite being widely used.
Drilling deeper into the issue, companies find that one major issue is their reliance on human judgment and manual investigation. Techniques like the “5 Whys” or Fishbone diagrams depend heavily on the experience and perspective of the individuals involved, which can introduce bias or lead to oversimplified conclusions. In many cases, teams may stop at the most apparent cause rather than uncover deeper, systemic issues.
Another limitation is the siloed nature of data in industrial environments. Valuable information is often spread across disconnected systems—sensor data, maintenance logs, control systems, and operator notes—making it difficult to comprehensively understand what happened. This fragmented approach can lead to incomplete analyses or missed correlations between events.
Time and resource constraints also play a role. Conducting a thorough RCA can be labor-intensive and slow, which delays corrective actions and increases the risk of recurrence. Additionally, traditional RCA struggles to scale in environments with high complexity, where multiple variables interact over time to produce a failure.
Finally, current methods often focus on reactive analysis—identifying causes only after a failure has occurred—rather than enabling predictive insights that could prevent issues in the first place. As industrial systems grow more complex and data-rich, these limitations highlight the need for more advanced, data-driven RCA approaches.
See also: 5 Real Ways AI is Transforming Day-to-Day Industrial Operations
The Role of Data Management, AI, and Generative AI in RCA
To overcome these challenges, many industrial organizations are beginning to adopt advanced data management, analytics, and AI-driven tools. These technologies can analyze large volumes of real-time and historical data to detect patterns, identify anomalies, and suggest likely root causes faster and with greater accuracy—enhancing the precision and speed of RCA while enabling more proactive maintenance strategies.
One way new technologies and mindsets tackle RCA is to start with an enterprise-wide data management strategy. In industrial settings, traditional RCA often faces challenges due to data silos, manual data gathering, and fragmented collaboration. What’s needed is a modern data management platform that addresses these issues by leveraging AI and a robust data management system to enhance RCA processes.
Specifically, what’s needed is an RCA strategy that uses modern tools and systems. Such a solution needs critical capabilities, including:
- Unified Access to Contextualized Data: Organizations need an interactive workspace where engineers can seamlessly access various data types—such as time series charts, P&ID drawings, 3D models, tables, and images. This integration facilitates a comprehensive analysis by consolidating previously siloed information, thereby reducing the time spent searching for relevant data.
- AI-Assisted Document Interaction: A suitable platform must incorporate AI capabilities that enable users to perform intelligent searches across extensive document repositories using natural language queries. Such a feature allows for rapid retrieval of pertinent information and the generation of concise summaries from lengthy documents, streamlining the data extraction process essential for effective RCA.
- Collaborative Analysis Environment: A suitable solution should support real-time collaboration by allowing team members to annotate diagrams, tag colleagues, and share insights within a centralized workspace. Such a collaborative approach ensures that analyses are easily referenceable for future investigations, promoting knowledge retention and continuous improvement in RCA practices.
See also: What are AI Agents and How Are They Used in Different Industries?
A Final Word on Modernizing RCA
By leveraging AI and comprehensive data management, organizations can enhance the efficiency and effectiveness of root cause analysis in industrial operations, leading to improved safety, reliability, and productivity.