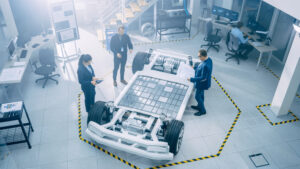
The shift towards hybrid-electric and fully electric vehicles brings new thermal management challenges. Automakers are turning to advanced design technologies, such as digital twins, simulations, and virtual prototyping, to address these challenges.
As the automotive industry shifts towards hybrid-electric and fully electric vehicles (EVs), manufacturers are facing new engineering challenges. One of the most critical challenges in this transformation is effective thermal management—the ability to control and dissipate heat generated by various components.
The complexity of thermal management in EVs is far greater than in traditional internal combustion engine (ICE) vehicles, given the high thermal loads of batteries, power electronics, and electric motors.
Increasingly, automakers are relying on modern design technologies, such as digital twins, CAD tools, simulations, and virtual prototyping, to address these challenges efficiently.
The Complexity of Thermal Management in Hybrid and Electric Vehicles
Thermal management in EVs involves maintaining optimal temperatures for various systems, such as battery packs, power electronics, electric motors, and more.
To put an EV’s thermal management issues into perspective, consider that EV batteries generate significant heat during charging, discharging, and acceleration. Keeping battery temperatures within a specific range is critical to maintain performance, extend battery life, and prevent thermal runaway.
Similarly, when it comes to power electronics, inverters, converters, and onboard chargers also produce heat while operating. If not effectively managed, excessive temperatures can compromise efficiency, lead to failures, or shorten the lifespan of these electronic components.
Given the compact designs of EVs and the integration of these systems within a limited space, thermal management becomes even more challenging. As such, manufacturers must find innovative solutions to handle heat dissipation and thermal optimization without compromising vehicle performance or safety.
Advanced Design Technologies for Thermal Management
To address these thermal management challenges, manufacturers are increasingly leveraging modern vehicle design and development technologies. Some of the key technologies automakers are turning to or expanding the use of include:
Digital Twins: Digital twins are virtual replicas of physical systems that enable engineers to monitor, analyze, and optimize thermal performance in real time. In the context of thermal management, digital twins allow manufacturers to:
- Model thermal behavior of battery cells, cooling systems, and other components across various conditions.
- Simulate thermal stress under different driving scenarios, from high-speed acceleration to long uphill drives, helping identify potential hotspots and failure points.
- Optimize cooling strategies based on data insights, testing different design options and materials in a virtual environment before physical prototyping.
This virtual testing not only speeds up development but also provides manufacturers with predictive insights that can be used to refine thermal management strategies throughout a vehicle’s lifecycle.
Computer-Aided Design (CAD) Tools: CAD tools are essential for designing thermal management systems, from developing cooling channels to integrating heat exchangers and thermal shields within a vehicle’s architecture. Modern CAD software enables designers to:
- Create 3D models of thermal components and analyze how they fit within the vehicle’s compact space.
- Optimize component placement to maximize cooling efficiency while minimizing impact on the vehicle’s weight and aerodynamics.
- Incorporate advanced materials with higher thermal conductivity or better insulation properties to improve heat dissipation.
By facilitating precise design and quick modifications, CAD tools help engineers create more effective thermal management solutions that can be directly integrated into production models.
Simulation Technologies: Simulation tools allow for rigorous thermal analysis, helping manufacturers evaluate the performance of different thermal systems under various conditions:
- Computational Fluid Dynamics (CFD) simulations are crucial for analyzing fluid flow and heat transfer within cooling systems. CFD can simulate airflow patterns and heat distribution across radiators, cooling channels, and battery packs, enabling engineers to optimize cooling mechanisms before physical testing.
- Thermal-Finite Element Analysis (FEA) tools simulate the thermal stresses that different components may experience over time. This helps in designing more resilient and long-lasting thermal management systems.
- Multiphysics simulations combine thermal, mechanical, and electrical analyses, enabling a more comprehensive evaluation of thermal interactions and heat management strategies across the entire vehicle.
Simulation technologies not only enhance the speed of development but also reduce costs by minimizing the need for physical prototyping.
Virtual Prototyping and Testing: Virtual prototyping enables manufacturers to create a virtual representation of the entire vehicle and its thermal management system. This approach allows for:
- Iterative design testing in a risk-free digital environment, helping engineers identify thermal inefficiencies and make design adjustments early in the process.
- Integrating subsystems, such as battery cooling, cabin heating, and power electronics, to evaluate how different thermal management solutions interact with each other.
- Validating designs against regulatory standards and safety benchmarks, ensuring compliance without the costs associated with physical crash testing or thermal failure testing.
Virtual prototyping can significantly reduce the time-to-market for new models while ensuring that thermal performance remains reliable and safe.
See also: Smart Manufacturing Essential for the Transition to EVs
A Final Word about Overcoming EV Thermal Management Issues
The shift towards hybrid-electric and fully electric vehicles brings new thermal management challenges. However, advanced design technologies, such as digital twins, CAD tools, simulations, and virtual prototyping, are helping auto manufacturers address these challenges.
By integrating these technologies into the design process, manufacturers can optimize thermal systems, enhance vehicle performance, extend component life, and ensure passenger safety—all while accelerating the development cycle.