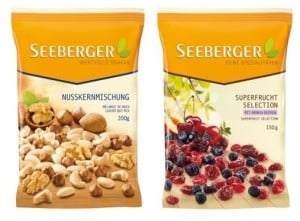
For inventory control and supply-chain management, food giant Seeberger built a “warehouse of the future” with Cisco WiFi and driverless vehicles.
Name of Organization: Seeberger
Industry: Processed foods
Location: Ulm, Germany
Business Opportunity or Challenge Encountered:
As a provider of snack foods and coffee, Seeberger understands the importance of moving inventory quickly to assure freshness and meet rising demand. Inventory is highly perishable, and with an international business, the company needed real-time views into its processes.
Seeberger is known for its great variety of food, consisting of dried fruit and nuts along with a wide variety of flavored coffees. Founded in 1844, the company has seen unprecedented growth in recent years. This past year, it took led the market in coffee roasters and market leader in dried fruit, with revenues exceeding $200 million. Sales abroad have also been accelerating. In 2015, Seeberger’s export business grew by 25 percent, with sales to France, Austria, Switzerland and China. The company’s trail mix cranberries have been an especially hot commodity in the Asian market. Seeberger also operates one of the oldest coffee roasters in Europe, and is a supplier to restaurants, hotels, restaurants, and workplaces.
As a result, the company’s production and supply-chain operations have extended beyond its headquarters in Germany to sales offices in Paris, Riga, and Shanghai. This continued growth has led to the need to build new warehouse facilities to house fast-moving inventory. Existing inventory control systems in the warehouse were too slow for the faster pace of the business. Managers did not have enough visibility into processes or potential issues. When an order came in, raw materials were manually retrieved and brought to machines. Assembly was too slow and not structured optimally.
The company was also challenged with improving its production processes, as well as making the best use of people and space.
How This Business Opportunity or Challenge Was Met:
To address the requirements of a “warehouse of the future” that provides real-time inventory control and supply-chain events, Seeberger turned to Cisco’s Blended “Internet of Everything (IoE)” solution set, designed to feed state-of-the-art storage and production processes.
The system was designed entirely over Cisco Wi-Fi with driverless transport vehicles (DTVs) operating 24 hours a day, seven days a week, 365 days a year. The new warehouse includes automated operations wirelessly linking orders, production, storage, and DTVs.
“To control production, storage, driverless transport vehicles, administration, and much more, we wanted wireless everywhere,” says Michael Nusser, deputy team leader, support and incident management for Seeberger. The network was built gradually, with the whole Seeberger campus now connected via Cisco wireless access points.
Warehouse operations are integrated and automated, and temperature and humidity in the raw goods warehouse are controlled. When a new raw materials order is created, the system notifies the stacker cranes in the warehouse. They fetch the various goods and take them to collection points, where a DTV picks up the pallet and transports it to one of 25 production machines. An operator with a wireless terminal scans the pallet with finished products. An order is created by the warehouse management system and relayed to the DTV so it knows where to store the pallet. The DTVs drive across bridges and around corners. They call lifts through the WLAN and are instructed to proceed after it’s safe to enter.
Measurable/Quantifiable and “Soft” Benefits From This Initiative:
As a result of this implementation, Seeberger has essentially what can be considered a warehouse of the future. All operations and processes run on real-time data, and managers can access data at any time. Previously Seeberger’s inventory managers could only document the storage of raw materials and finished products, or in other words, the start and end of the production process. All the steps in between are now combined by integrating more devices, such as handheld terminals that leave a digital trace.
Real-time visibility is a key part of the process. “We know exactly where specific goods are at any stage and have detailed information about the entire production process,” says Florian Paul, deputy manager of IT infrastructure at Seeberger. “Food traceability is no longer a challenge.” For example, if a pallet of raw materials hasn’t been opened by the end of a shift, a DTV is notified wirelessly and carries it back to the temperature-controlled storage area.
Remote access is also facilitated as well. For example, technicians checking sprinkler systems can record results anywhere throughout Seeberger’s facilities. Potential new projects include using the WLAN to feed production data directly into the ERP system to improve resource planning.
(Source: Cisco)
Want more? Check out our most-read content:
Research from Gartner: Real-Time Analytics with the Internet of Things
Getting Fast Results from Slow Data
Goodbye Don Draper, Hello Big Data: An EMA Report on Modern Analytics
Why Edge Computing Is Here to Stay: Five Use Cases
What’s Behind the Attraction to Apache Spark
Video — Plat.One CEO: Enterprise IoT Doesn’t Have to Be Hard
Liked this article? Share it with your colleagues!