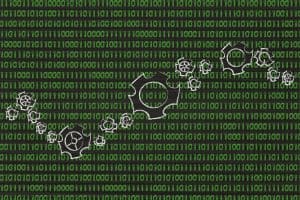
IoT and sensor data that is made available remotely via wireless connectivity can be analyzed to look for trends and enable proactive maintenance.
As we emerge from the pandemic, companies are realizing many of the lessons learned should become standard operating procedures going forward. Nowhere is that more apparent than with servicing and managing equipment and products in the field. Fortunately, technology that allows organizations to remotely monitor the performance of their equipment in the field in real-time can play a significant role. The benefits of having that information can be complemented by using predictive analytics on that data to spot problems in the making. That allows corrective actions and proactive maintenance to be taken, eliminating downtime or the need for an unscheduled site visit.
There is no doubt the pandemic hammered home the need for product manufacturers and companies that service products in the field to revamp normal operating procedures. Travel restrictions prohibited sending people far and wide to assess and fix problems. Even if people were local and could theoretically visit a facility, the local government or the company itself might have disallowed anyone from entering a facility.
Technology elements for transformation
Such obstacles during the lockdown highlighted the need to have real-time insights into how products are operating in the field. The way to do that is to make use of several technologies together.
What’s needed first is embedded sensors in the products to monitor and measure current conditions and key performance indicators (KPIs). Parameters measured might include operating speed (e.g., of a motor), temperature, or pressure. It could also include things like the status level and consumption of consumables such as ink in a printer, oil in an engine, the film in an imaging system, and more. Fortunately, the wide-scale embracement of smart sensors and the Internet of Things (IoT) provides the necessary technical underpinnings for such data access.
In the past, such data was only available on-site and only accessible in industrial control systems (ICS) such as supervisory control and data acquisition (SCADA) systems or distributed control systems (DCS). Typically, the sensors were hard-wired into such systems over a private on-premises network.
The growing use of existing wireless services such as Wi-Fi and 3/4G cellular and emerging wireless connectivity services (e.g., Wi-Fi 6 and 5G) can make that data more widely available. Such connectivity can allow other systems, besides ICS systems, to access the data. And the wireless connectivity can be used to allow remote access to the data as well. So now, an organization that supplies the equipment or manages it can centrally monitor the state of the devices in the field. Remote access to such data can be used tactically. For example, many organizations have used such capabilities to move from reactive maintenance (fix it when it breaks) to preventive maintenance.
The final piece in the technology trifecta is analytics. The IoT and sensor data that is made available remotely via wireless connectivity can then be analyzed to look for trends.
Reducing downtime, optimizing performance
Using sensors and connectivity lets product manufacturers and the companies that service products in the field transition from calendar-based maintenance to condition-based monitoring and maintenance. A company might use historical data to find that vendor A’s part typically lasts twice as long as the manufacturer’s stated mean time to failure in the company’s facility. So, rather than replace it on the manufacturer’s schedule, they could confidently get extra use out of the piece. That spreads parts replacement cost out over longer times, reducing overall annual spending for spare and replacement parts.
Even more, is possible when predictive analytics are used on the data from the sensors. For example, a company manufacturing or servicing a product might find that a rapid, 20% spike in operating temperature is a precursor to the device failing in five days.
That’s just the beginning. The combination of sensors plus connectivity plus predictive analytics allows a proactive approach to maintenance that lets companies cut costs, get more life out of installed equipment, and reduce downtime.
As noted, companies in the past would routinely replace a part based on a set maintenance schedule. With performance insights from the device or part, a company can see for itself whether the unit is exhibiting signs of performance degradation. Such predictive capabilities that detect potential problems allow companies to fix problems in the making before an outage and deliver additional savings in cost avoidance. This avoids unplanned downtime. And it can avoid the expense of conducting emergency repairs. Dispatching technicians with no notice incurs high travel costs. This break/fix model of implementing repairs requires expediting parts to the site, which results in high shipping and delivery fees. All of that can be minimized with analytics-derived performance and status insights.
A prime example of the value of such capabilities is the work being done by Howden, a global leader in manufacturing air and gas handling solutions. Their equipment is used in sectors including infrastructure, power generation, oil and gas, wastewater, metals, mining, and transportation.
The company developed the Howden Uptime solution using ThingWorx from PTC, which offers an IoT platform, designed to accelerate digital transformation. The Howden Uptime platform is a remote performance monitoring and optimization application used for any kind of rotating equipment (compressors, fans, turbines, etc.) running in customer facilities all over the world.
It can proactively monitor and manage devices running in remote locations, some of which are in the North Sea and other remote locations. This solution lets Howden watch its machines as though they are standing beside them.
Enabling new business models
By imparting connectivity to equipment, a manufacturer or company servicing the equipment can transform its operations and business model.
It can move from reactive to predictive operations, thus increasing maintenance staff efficiency and reducing unplanned downtime.
Most importantly, connectivity technologies and the data collected are essential to take part in future industry initiatives such as Industry 4.0 and digital twins.
Why is this important? The companies moving forward with Industry 4.0 and digital solutions are better positioned to weather economic disruptions. They can move faster and further than their peers during a crisis. Such an advantage is not lost on the industry as it emerges from the COVID crisis.
To learn more about enabling connectivity and analytics to monitor and support equipment visit: www.ptc.com/predictive-analytics