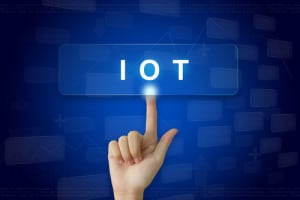
With IoT, manufacturing plant managers have way more opportunities to implement better operations with increased productivity, flexibility and, quality.
Due to IoT, managers have an excellent opportunity to implement better operations through increased productivity, flexibility, and quality. To reap the most benefits requires more effective connectivity and a better flow of information between all the different data-producing and data-consuming devices, systems, processes and people within a company.
Manufacturing plants are operating at a much larger utilization capacity than in the past. Often, they are a 24/7 type of operation. With downtime costing plants up to $20,000 per minute, they can’t afford to have any disruptions to their processes.
Manufacturers have to deal with many different challenges. They are in need of more flexibility within their manufacturing process, if they want to meet the demands of their evolving consumers. They are faced with the continuous pressure to keep up with increased demands from limited CapEx spending, and in many cases, they are relying on existing resources and assets. These manufacturers need improved access to data in order to make better decisions in regards to where to invest, and they would like to have access to leading-edge experts. However, they are faced with the problem of limited resources and aging workforce problems.
See also: What is the role of standards, big data, and analytics in today’s manufacturing?
IoT is one piece of an even bigger puzzle, the large transition that’s been occurring for a while now in manufacturing. More machines inside plants are being connected by utilizing the technology that runs the Internet.
Things are being embedded with intelligent sensors and gaining the ability to communicate. These are not merely sensors for measuring temperature, pressure, humidity, and other parameters. They can include almost anything. For instance, a camera can become a sensor, and it can be used to track movement, quality, or temperatures by using infrared imaging. This all leads to a more intelligent manufacturing environment.
Connectivity is moving even further along, beyond plant controllers, and on to other factory assets, including robots. These other connected things are being used to better understand all the factory’s complex processes. More intelligent machines can be controlled more easily, which increases efficiency. Many people refer to this as, “plant-wide optimization.”
Bringing connectivity and analytics to the manufacturing process
When it’s successful, IoT is usually a combination of connectivity with real-time analytics and new cloud services, which results in improved manufacturing output, better uptimes, more flexible manufacturing, and reduced costs from the consolidation of siloed systems and proprietary networks. However, the new focus has now become protecting these new architectures from cyber attack. The connection of all these devices to the entire enterprise is an understandable goal, but it comes with more risk of attacks.
For those who believe in the power of IoT inside factories, some important goals they are looking to achieve include lowering the total cost of ownership, improved operational responsiveness, reduced time to market, and protecting important manufacturing systems. IoT aids in all these goals.
Connectivity has been on an upward trend for several years, and it has transformed cars into connected vehicles and transformed televisions, along with many other things. However, IoT has made the largest impact on the business side of a company’s operations, allowing manufacturers who leverage IoT to substantially improve core processes in business enterprises.
Companies appreciate and desire technology that enables them to acquire and analyze the influx of large amounts of speedy data. This kind of connectivity that is created by IoT allows companies to focus less on cost and more or growth. Leaders who are advocating for and utilizing IoT as much as possible are thriving and experiencing the benefits of new growth opportunities.