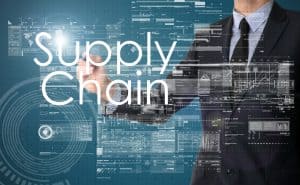
Those who adopt a technology-led recovery strategy now will avoid shortages this year.
The holiday season was like no other. From turkeys to iPhones and sportswear to alcohol, it seemed almost everything was in short supply. In fact, a recent report from Adobe Analytics predicts U.S. online holiday spending is expected to grow at its slowest pace in at least eight years, as product shortages, higher prices, and lingering pandemic-related uncertainties threaten to put a strain on the shopping season.
Why has this been a wake-up call for businesses and consumers?
It’s been a frenzied year for supply chains globally, and the supply chains in North America have not been an exception. From COVID-19 vaccine production to the container vessel stuck in the Suez Canal to auto chip shortages—events this year have really thrown global supply chains under the public spotlight.
Does JIT need a re-fresh?
Businesses must become more dynamic with agile supply chains or risk shortages that jeopardizing brand reputations and, more importantly, the customer experience. Our supply chains are much more fragile than they were in past years. New risks need to be factored into continuity plans, and that means moving from just-in-time (JIT) manufacturing to a more dynamic, demand-driven supply chain environment. Ultimately, businesses must revaluate entire value chain operations to understand where technology, processes, and people can help anticipate future issues.
CX needs a re-fresh, and it starts from the top
The takeaway for many organizations is to focus on building greater resiliency in their own supply chains through identifying and tying in the key inflection points of success or failure across the entire value chain of their operations. These inflection points are directly connected to an organization’s impact on the customer experience, meaning they bolster or damage a brand’s reputation.
This means thinking service-first. A service-first mindset gives a more holistic understanding of processes and technology and their effects on customers, assets, and employees. This also allows organizations to track those key inflection points and take pre-emptive action before it’s too late.
For this approach to succeed, it demands executive-level management to prioritize and be engaged to drive this way of thinking and enable the investments required. As so very often in these business process shifts, it must start from the top.
Should we be hopeful that the Holiday session will return to normal in 2022?
Recovery will, of course, not be immediate, with many forecasts being measured in years rather than months.
But preparing for supply chain resilience today makes strategic sense for businesses, employees, and end-customers going forward. For those who adopt a technology-led recovery strategy now, I predict shortages will be avoided and we’ll have a holiday season filled with plenty of presents under the tree.