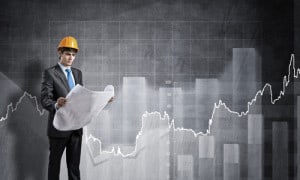
If you deal with industrial assets, industrial analytics in IIoT applies to you. Here’s what you need to know – from connecting assets to the edge analytics
Enterprises in various industries are pushing forward in their journey to digitalize operations and businesses. As part of this digital transformation, many seek to leverage the Industrial Internet of Things (IIoT) technologies to connect to assets such as machines and control systems. With this extended connectivity, enterprises can now integrate the assets with business applications, enterprise information systems and people to optimize business processes or to create new business opportunities.
Clearly, IIoT is a strong enabler for digitalization. If you’re dealing with industrial assets, IIoT applies – whether it is in the operations of infrastructure equipment such as wind turbines, locomotive engines, large port cranes, or in productions and manufacturing settings.
Connecting to the Assets
In the process of building an IIoT system, the first set of issues is how to establish connectivity to the assets: the types of communication technologies to use, data interoperability (e.g., how to collect data from a PLC), the type of gateways to deploy if needed, and how to secure the data and systems once they are connected. Obviously, solving this set of issues are the important first steps and the visibility to assets’ operational states brought about by this extended connectivity, often remotely, offers great value by itself.
In fact, this is nothing fundamentally new – in many industrials, enterprises have been building and using similar connected systems in both the operational and production environments for a decade or more, many being enabled by the traditional machine-to-machine (M2M) communication technologies. For example, in industries such as rails, subways, wind farms, power transmission and distribution, supervisory control and data acquisition (SCADA) system have been used to acquire and manage data from the assets and to provide supervisory functions based on the data.
[ Related: The Future of the Industrial IoT Is Growing in Testbeds ]
In other industries such as petroleum, chemical or nuclear power generation, distributed control systems (DCS) have been used to collect data from control systems and perform process control. In discrete manufacturing of aircraft, automobile and other large machineries, manufacturing execution system (MES) have been increasingly used to collect data from the production machines and about material and part supply and worker performance as well to orchestrate production processes.
Industrial Analytics: Beyond Visibility
Driven by the Internet, the advances of technologies in communication (e.g., the IP stack supported by high bandwidth and low cost wireless technologies) and computation (e.g., cloud computing, big data, machine learning frameworks) have made the building of connected systems more feasible and affordable.
What is important in IIoT, however, is the new capability to apply advanced analytics to the large volume of data collected from the connected machines and business processes. From the analytics, enterprises will be able to gain new insights into the operations and a new ability to use these insights to optimize the running of the machines and business processes, and to open up new business opportunity.
Just like internet companies that can create high value by optimizing the commercial assets in the consumer market by data analytics, industrial enterprises should and can also generate high value by optimizing their industrial assets from analytics of machine and processes data they have acquired from the operations and productions.
It’s often said that data is the new oil. In transforming machine raw data into actionable insights, industrial analytics plays a crucial role in IIoT just like refineries that turns crude oil into high energy fuel. The actionable insights from the analytics is the fuel that drive the optimization of industrial operations and production, the creation of new revenue streams and the ennoblement of new business models.
IIoT and Industrial Analytics Enhance Industrial Systems
IIoT systems are not for replacing exiting SCADA, DCS or MES systems or the control systems they supervise/orchestrate but to enhance and support them by providing actionable insights to make these processes more intelligent and automatic. For example, existing SCADA, DCS and even MES tend to rely on human operators in the loop to be informed of events and to respond to them.
Analytics in IIoT systems would help these systems moving from being just descriptive (and reactive) to predictive and even prescriptive in response to events. It will also help to automate increasing number of tasks such as anomaly detection and fault diagnostics that are typically performed by human operators today. When building a new generation of SCADA, DCS, MES or similar M2M systems, IIoT technologies in communication and computation frameworks and capabilities such as industrial analytics may be incorporated into their designs.
Comparing to their older sibling of business analytics in the commercial settings, industrial analytics has unique requirements and challenges. Because of the potential physical effect that may produce when analytics results are applied to the running of the assets, industrial analytics has strong requirements in safety, security and reliability. It also has more stringent expectation in correctness and performance (e.g., in its responsiveness (timeliness) to events that are being detected.
These set of unique requirements, especially those in safety, call for strong governance in how analytics results should be applied and what minimum measures must be in place to safeguard the “do no harm” principle. The specificity and level of these requirements vary depending on the individual IIoT applications. To questions such as what architecture to support industrial analytics (e.g. cloud or edge) and what analytics techniques to use to satisfy these requirements, there is no one-size-fits-all solution.
Industrial Analytics Architecture: From Edge to Cloud
Take analytics architecture, for example. The simple notion that all analytics be performed in the cloud works for some but not all IIoT applications. Given the security, reliability, performance (e.g., in latency) and even cost (e.g. in wireless data bandwidth), the general architecture for analytics would likely be distributed across the various tiers of systems, from edge (near where the assets are) to the operation and control centers, enterprise datacenters (or private clouds) and the (public) cloud (e.g. Amazon’s AWS and Microsoft’s Azure).
[ Related: How to Get the Most From the Industrial IoT ]
It make good sense to place analytics near the data sources and the locations where decisions to be made and actions to be taken based on the analytics results. Performing analytics locally this way helps to restrict the scope in which sensitive data may be exposed, and limit the network span that data and information need to travel back and forth. This latter aspect in turn generally help to increase reliability and reduce latency. Placing analytics near the assets (the data sources) may also enable high-fidelity data collection without incurring excessive cost in bandwidth in the case wireless communication is used.
This approach of edge analytics does not exclude sending data or information to the next tier of systems. Generally, however, the higher the tier in which these systems are, the higher level of summary information they may need and the less stringent responsiveness they may require. Therefore, moving up the tiers of systems, both the temperature (the level for responsiveness) and the volume of the data tend to go down.
Computing resources, however, tend to be more constraint near the edge and richer in systems in higher tiers, and abundant in the cloud. In some situations, such a fault has been detected at the edge and additional analytics for identifying and diagnosing the fault require computational resources beyond those available locally at the edge, an optimal analytics architecture should be able to direct the machine data, on-demand, be sent (temporarily opening a “firehouse”) to computation resources in the next tiers (e.g. where a cluster of servers may be available) so that the more demanding analytics can be performed timely.
Furthermore, analytics model building requires both large amount of high fidelity data and large computing power to train and validate the models. This exercise is typical carried out on-demand or on-schedule in a batch mode, so it deals with “cool” data. Therefore, when designing an analytics architecture, consideration must be given to how to allow the collection of machine or process data at the edge and make them available to systems (e.g. in enterprise datacenters or the cloud) where sufficient computing power is available for model building. (When taking these data to the public cloud, some desensitization on the data may need to be performed.)
Analytics Models for Streaming and Batch Analytics
Beyond simple statistical analysis of data to give summary aggregated views of the operational states and performance across temporal-spatial or organizational dimensions (e.g. production lines, plants, factories and so on), advanced analytics (such as those needed for predicative maintenance) tends to require building analytics models based on data.
There are two major categories of analytics models depending on whether how strong causality is used in model building processes. The first type, known as first-principle-based or physical modeling, relies on the laws of physics and chemistry to construct models with strong causal relationship, and the second type, loosely termed, statistical modeling, mines the relationship hidden in the data to build models to predict events and make inferences from new data, often with weak or uncertain causal relationship.
The physical modeling requires deep domain knowledge of the construct and internal working of the machines, and thus tends to be more complex and involved to build and could be more brittle when parts and components change. Physical models are often used in the traditional conditional based maintenance. Statistical modeling places more reliance on the data themselves though any level of domain knowledge would help the convergence of the exercise and the verification of the models.
[ Related: Industrial IoT Risks You Shouldn’t Ignore ]
With the advances in machine learning techniques and more abundant computing power, the role of statistical modeling in IIoT is expected to increase. On the other hand, as more products are designed, engineered and manufactured through integrated digital processes including simulation, that level of difficulty and the cost of building physical modeling may be reduced over time as well. At the end, it is reasonable to expect that physical and statistical modeling will play hand in hand complementary each other in IIoT.
The models, once constructed, are deployed into the IIoT analytics runtime systems. These systems use the models to capture meaningful patterns as they occur in streaming data from machines or processes so that events can be responded timely to by the operational or production systems. This is the essence of streaming analytics – in contrast to batch analytics, it is performed continuous and timely.
Analytics models can also be used to analyze data across operational stages to identify process bottlenecks and causes of inefficiency. This type of analytics is typically performed in the batch mode – on-demand or periodically. For example, analysis can be performed across different product lifecycle stages from design, to process and production engineering, and the manufacturing process to identify ‘impedance’ between these stages so that cycle of introducing new products can be reduced.
As another example, historical data from the manufacturing processes about production machine conditions, parts and material used, workers and shifts can be used to identify product quality issues and their root causes. These types of batched oriented analyses are likely to involve large amount of heterogeneous data and are more effective to be performed in big data platforms.
Industrial Analytics Means for Business
In considering an IIoT system, it is important to have a clear understanding of what business value the system is intended to bring about. The business value may be for improving asset performance (e.g. increasing uptime), reducing maintenance cost, improving energy efficiency, optimizing production processes, enhancing product quality, or enabling new business opportunity through the connected products after being delivered and deployed. The specific details of the business drivers would guild the establishment of requirements and system design. In any case, industrial analytics should be considered early in the process as what analytics in the IIoT is required to deliver the business value and how to implement it.
A few examples of application of industrial analytics are included below:
- Predictive maintenance: enhancing and extending the decades-old condition-based maintenance by making it more affordable and thus its application more widespread. It can be part of a larger Asset Performance Management application.
- Production process optimization: the continuous monitoring of production outcome near real time based on analytics models (taking physical measurement and process control parameters as input) and provide feedback to process control to achieve optimal production outcome by fine tuning control parameters
- Production online quality optimization: the continuous monitoring of product quality as products progresses from work cell to work cell in a production line to detect early signs of defect so downstream work for defective products can be terminated as early as possible, or to adjust process control parameters to automatically prevent the defects from recurring.
- Asset usage optimization: the continuous monitoring the asset operation states and environment and dynamically providing feedback based on analytics models to control process to optimize the asset’s operation (e.g. wind turbines).
Note: The Industrial Internet Consortium (IIC) recently publishes a technical report, Industrial Internet Analytics Framework (IIAF) providing a first comprehensive survey of the unique requirements, challenges and applicable technologies of Industrial Analytics. For those who are interested in details of the topic, the IIAF can be a useful reference.”