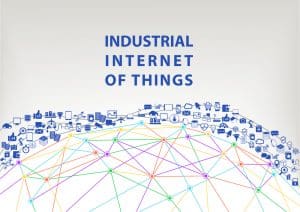
Survey finds 84 percent of enterprises cite monetization of product-as-a-service-revenue as the most important value/benefit of IIoT.
Manufacturers place a high value on Industrial Internet of Things (IIoT). However, they are encountering serious difficulties in unlocking the value of their innovation across their organizations, according to a new survey.
Software AG surveyed* over 125 North American manufacturers, primarily in the heavy industry and automotive segments, about where they are in the IoT Innovation Curve, and the results were startling.
Optimizing production is still important with just over half (58 percent of heavy industry and 50 percent of automotive manufacturers) seeing cost reduction as a major IoT benefit.
See also: Integration and IoT? Two Sides of the Same Coin
But this is put in the shade by the 84 percent of enterprises agreeing that the most important area of IIoT is “monetization of product-as-a-service-revenue.” That is innovative digital services are recognized as a future source of revenue and profit, and I would argue that this will be the primary source.
According to the German Government (and Germany knows something about cars), the day is coming when digital devices, tools, and of course software will account for 50 to 60 percent of the value of a car. The battery alone will account for 20 percent of the value of the vehicle.
The Bumpy Road to Fulfilling IIoT Technology’s Promises
Ownership of this digital service layer is paramount. An enterprise cannot afford to let faster-moving competitors dominate their customer base, offering an ever-increasing portfolio of digital services, while they focus solely on better wing mirrors or gearboxes.
The good news is that this has been recognized by U.S. industry. It has seen the Promised Land. So, what is holding it back?
First and foremost, integration. IT-OT (Information Technology and Operations Technology) integration is considered to be one of the most difficult tasks – with 57 percent of automotive manufacturers stating that this has prevented them from realizing full ROI from their IIoT investments.
Second, either complex tasks have either become much simpler to execute or simple tasks are seen as very difficult. Leveraging Predictive Analytics was reported as being only 2 percent more difficult than leveraging condition monitoring.
Manufacturers place a high value on IIoT, but they are encountering serious difficulties in unlocking the value of their innovation across their organizations. The survey revealed that the vast majority of manufacturers report that their IIoT investments are limited – locked in one small department or sector of their company – preventing these organizations from sharing the power of IIoT across their enterprises.
Our Chief Product Officer calls this the “Fractured Enterprise.” In the Internet of Everything economy, the fractured enterprise cannot even hope to compete. Half answers from disconnected enterprise assets result in ill-founded decisions or business reaction times that are too slow to be effective.
This has caused these manufacturers to lose millions of dollars in potential profits as they fall behind more forward-thinking competitors that have invested in predictive analytics and innovative integration strategies that scale IIoT across the enterprise.
Best Practices to Achieve Success
These are not insurmountable problems. There are five best practices for manufacturers to follow when looking to scale their IIoT investments across their enterprises:
- Scalability by design not as an afterthought – with clear collaboration between IT and the business, using a step-by-step approach with a clear focus on near term and long- term objectives
- Create a transparent, synchronized roll out process and don’t let other plants or departments jump the gun
- Give IT the ability to connect at speed with a digital production platform that is proven to be successful
- Minimize bottlenecks by leveraging a GUI driven, consistent platform to enable an ecosystem of IT associates, business users, and partners, to develop business applications and
- Enable the plant or field service workers to work autonomously without continual support from IT through GUI-driven analytics, centralized management and easy, batch device connectivity and management
And start with integration. Total integration is what makes a fractured enterprise whole, and total integration – on-premises, in the cloud and at the edge – is the only way to build successful IoT architectures, landscapes or applications.
To paraphrase our CPO again: To prepare for IoT, Industry 4.0 or a digital future, the enterprise must integrate, integrate, integrate. It makes the whole greater than the sum of the parts.
*The Software AG IIoT Implementation survey was completed in Q2 2019 by Software AG and an independent third-party research house. The survey queried nearly 200 respondents at large manufacturing companies across automotive, heavy industry, high-technology, electronics, pharmaceutical, and medical device industries. The respondents were primarily senior executives leading Manufacturing or Information Technology with the breakdown of 50% Managers, 38% Directors, and 13% Vice Presidents or higher.