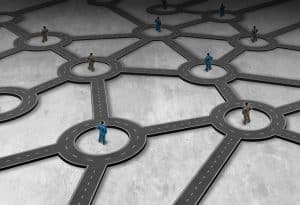
At the heart of the supply chain digital twin development lies a flexible supply chain simulation model that is data-driven and scalable.
What does it take to build the digital twin of a supply chain network? As supply chains are very complex with many moving parts, replicating the network and associated systems in augmented reality isn’t an overnight task. Late last year, a team at SAS put together a digital twin of a supply chain, and explained how the pieces fit together.
With such a capability, a supply chain’s digital and physical counterparts “are synchronized at a specified frequency and fidelity,” according to Bahar Biller, senior operations researcher at the SAS Analytics Center of Excellence. “The goal of the supply chain digital twin is to mimic this flow to predict various KPIs and gain visibility into the future of the supply chain operations; assess the impact of operational policies and investment decisions in a virtual environment; and stress test the supply chain and identify the best courses of action to take when faced with disruptions.”
Download Now: Building Real-time Location Applications on Massive DatasetsSAS’s digital-twinned supply chain architecture supports the following processes:
Supply chain network flow: “At the heart of the supply chain digital twin development lies a flexible supply chain simulation model that is data-driven and scalable with the number of suppliers, factories, warehouses, and customers,” says Biller. “Warehouses replenish finished goods inventory from factories whereas factories replenish component inventory from their suppliers. Each of these events must happen at the right time for the right quantities. Thus, there is a complex logic to the network flow moving both forward and backward. It requires the implementation of plans to manage suppliers, production, transportation, and inventory throughout the supply chain.”
Collect all relevant information and data which fully describe the supply chain: “Combining supply chain network flow with all necessary pieces of information and data completes the characterization of the supply chain logic — to mimic the flow of thousands of products,” Biller continues. Potential input data sets may include the following:
- Supply contracts and supplier data
- Initial inventory
- Production plan
- Customer demand
- Transportation details
- Inventory control policies
- Supply chain cost parameters
- Characterization of disruptive events (e.g., loss inventory and/or capacity due to natural disasters or disturbances)
Build in scenarios for random events: “The representation of the supply chain logic is followed by the characterization of the uncertainty in the random supply chain inputs,” says Biller. “Examples of random inputs include supplier lead-time, production and assembly times, transportation time, and customer demand size.”
Design “what-if” games: Specify “the levers that the client could be changing in the search for better ways to manage the supply chain,” Biller advises. “If the purpose of developing the supply chain digital twin is to help improve the management of inventory, then the levers could be chosen as the inventory control parameters. If the goal is to support fleet management, then the levers would likely be chosen as the attributes of the transporters. The lever selection could be further customized to support supply chain reconfiguration decisions.”
Deploy: The digital representation of the supply chain is executed, and in the process, “generate vast amounts of data representative of how the supply chain might perform in the future,” Biller states. From this, risk profiles can be developed to calculate and predict supply chain fill rate and the total cost. “Therefore, not only do we predict the expected values of the two key supply chain KPIs, but we also quantify the risk in their predicted values.”