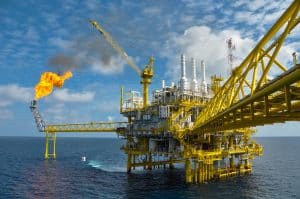
Digital twins are being deployed in different industries to address remote workforce operational challenges and even to train new employees before they set foot in the workplace.
The COVID-19 pandemic is drastically changing the telecommunicating landscape, and Global Workplace Analytics already predicts that 25 to 30% of the total workforce could work remotely multiple days a week by the end of 2021. Increasingly, organizations are implementing digital twins to address the new challenges introduced with such a change in operations.
But what is a digital twin? While there are many definitions, the term “digital twin” used in this article refers to a digital replica of a physical entity. A digital twin contains all the information that composes the historical and current configuration. In terms of deployment, digital twins can be designated for specific projects to accelerate program timing, or they can be created to improve overall business performance.
See also: What is Digital Twin Technology? (Sponsored)
While this technology may be new to some, a Gartner survey of companies from various industries across six countries found that 75% have already implemented or plan to implement a digital twin within a year, proving that digital twins can be used beyond typical industrial IoT use cases to creatively enhance various digital environments and innovate new services.
Meeting the challenges of the remote workforce
Many organizations and industries are set up to successfully handle the changed workforce, as well as monitor and drive operations remotely. However, others are plagued with misconceptions about remote solutions and are finding what they have implemented isn’t working.
For example, in industrial fields like manufacturing, there is a misconception that traditional monitoring and control mechanisms like a Distributed Control System (DCS) or a Supervisory Control and Data Acquisition (SCADA) platform contain all operational data and that connecting these systems enables remote data access for visualization and analytics. In reality, however, only 50 to 80% of remote operational data flows through SCADA and DCS, and in many cases, there is no instrumentation that provides remote access.
Furthermore, there are other industries that need to digitize their data so they can access it and manage it remotely in order to make real-time operational decisions, increase situational awareness, and improve productivity. At the same time, they need to support a remote workforce since COVID-19 has limited the number of personnel physically allowed in a space.
One solution that more organizations are implementing is the use of digital twins to not only digitalize operations, but also help to reduce operational risk and meet compliance regulations.
Companies that had already started their digital transformation and had leveraged these digital technologies to evolve cultures and work processes were much better prepared when stay-at-home orders were in place.
While digital twins comprise transactional data like maintenance records, they also host real-time information, process simulation, geospatial data, time series data, and visualization and analytics. With this information, users can troubleshoot, identify root causes, proactively respond to trends, provide emergency response, run simulations, and provide remote support, saving the user time and money.
Applications across industries
Digital twins are being deployed in a variety of different industries like oil and gas and manufacturing to help monitor plant and factory operations as well as increase revenue and productivity among a growing remote workforce.
For example, digital twins can be used to train new employees on work operations before they even set foot in the workplace.
Ship operators of international cruise lines need to be familiar with the ship and its equipment to operate it effectively on the first day at sea. But since there aren’t always ships available, new hires have to wait months until they return to shore before being trained on the vessel.
One large, international ship builder decided to deploy a digital twin to solve this problem for naval ship operations. After uploading the 200-page operating manual, over 6,000 drawings and 10,000 videos to the digital twin, the ship builder was able to use a digital twin to generate 3D simulations of assets that were connected to real-time data from the ship. These simulations gave trainees the ability to understand causations as well as the effect of the change or repair without ever touching a piece of the onboard equipment, resulting in a more efficient, timely ship operator training program.
Operationalizing tasks
Digital twins are frequently being used in this manner to operationalize tasks. The same Gartner survey found out that 88% of digital twin deployments run simulations. Further, over half of digital twins will be integrated with other digital twins, creating a comprehensive digital twin of an industry’s entire operations with the latest evolutions of each physical asset.
Alternatively, digital twins can be used to help configure the logistics of a construction project.
One American university used a digital twin to decide the most cost-effective, sustainable approach to reach a building’s optimal performance level. The university developed a detailed control estimate that revealed how much it would cost to reach optimum performance and the benefits gained by reducing long-term operating costs. This effort resulted in $321,834 in annual savings from energy and $19,671 savings from the Social Cost of Carbon.
And although, as a company, you hope it never happens, a digital twin can also be vital when remotely navigating an emergency.
An ultra-deepwater offshore drilling rig company experienced an explosion that resulted in irreparable environmental and plant damage. When regulators began to investigate the incident, they asked for information on the blow-off valve control system, which is responsible for releasing engine pressure. At the time, there were no requirements for storing information onshore, and all the drilling company’s maintenance records, drawings, and operating data were on the rig itself. While the company had access to some drawings, they were unable to determine which the most up-to-date version was.
Now, there is a requirement for onshore data storage as well as a requirement for a third party to inspect blowout preventors prior to operations at deepwater offshore drilling plants. By implementing digital twins, these third parties can remotely monitor all real-time data and can fix equipment from 10,000 feet away to prevent potential disasters from occurring.
Nonetheless, the obstacle for implementing digital twins is often digitalization itself. Not all industries have been forced to implement real-time, remote monitoring like the offshore oil and gas industry. It can be a large ask to convert the spreadsheets, drawings, and various analytical tools that a company utilizes every day and put them into a comprehensive digital model that can be recorded, referenced, and revised remotely.
However, digitalization does not need to be a large, overwhelming process. Digitalization must provide an easier job for employees, instant results, and an easy-to-learn system. Digital twins cannot operate effectively without advanced technology around them. So, by starting small and taking steps in the digital transformation process by investing in technologies like AI, intelligent sensors and assets, advanced analytics tools, and machine capabilities, an individual or team can better propose a funding for a larger digitalization project. Implementing a digital twin will help the larger company better understand the value of the enhancement.
The need for digitalization has never been more apparent than in a nationwide pandemic that requires employees to work apart from one another. By starting the process now, companies can be better prepared for future situations that may come their way.