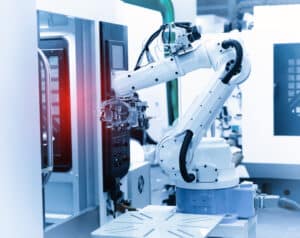
Virtual commissioning saves time and money, and it avoids interruptions of existing work cells, production lines, and plants.
Virtual commissioning of production line and manufacturing plant equipment has been envisioned for decades. Finally, essential technologies like digital twins, sophisticated simulations, and modeling are available, allowing auto manufacturers to reap its benefits.
Why all the interest in virtual commissioning, and why now? Several factors are at play.
There is the increased use of intelligent automation with many more self-thinking machines on production lines. Those evaluating aspects of work cells, production lines, and entire plants with the goal of improving efficiency and reducing costs often look for ways to automate tasks with smart equipment. The wide-scale embracement of AI and ML is making such systems smarter (yet more complex).
As a result, more aspects of manufacturing are increasingly automated. The end result is that manufacturers are looking for ways to do much of the work using either standalone robotic systems or systems where a human and robot complement one another in completing a task.
Another factor making virtual commissioning more important today is that auto manufacturing has fundamentally changed in recent years. Production cycles are shorter, giving manufacturers less time to plan, develop, and deploy production line systems for the next model car.
Additionally, much more customization and personalization are required in the industry today. Customers have high expectations and want specific features and capabilities. As a result, auto manufacturers must support this by modifying their traditional production methods to allow a single production line or plant to build and turn out hundreds of variants of their models.
Virtual commissioning of equipment can help in all of these areas. With virtual commissioning, an auto manufacturer would start with a digital model, a digital twin, of the piece of equipment or system. The model would also include the equipment’s controller code – specifically, the programmable logic controller (PLC) code. Finally, there would be a virtual development environment that lets the two run together and allow simulations of their interplay.
Using such virtual representatives of new equipment lets manufacturers test their systems to better understand how they would fit into an existing environment or how they would perform in a new cell, line, or plant. In this process, aspects of the system, including motions, sequence of steps, PLC software execution, and more, and be optimized before anything is installed on a new line or changed on an existing one.
A most important characteristic of using virtual commissioning is that a manufacturer can see not only how that new equipment will perform but how it works with other elements in a production process. Advanced implementations of virtual commissioning use that information as part of broader modeling and simulations to test different strategies and optimize end results.
For example, suppose one step of a manufacturing process currently requires human inspection for defects. A manufacturer could compare different alternative systems, such as a 100 percent robotic system that uses machine learning and AI to detect defects versus a solution that provides an AI-based inspection assist to the human, who still makes the final decision. The simulations could help evaluate the effectiveness of one approach versus another and provide details about the cost comparisons of the different methods.
See also: Digital Twins, IT/OT Convergence Drive the Industrial Internet
Benefits and use case scenarios for virtual commissioning
Without virtual commissioning, any mechanical and programming problems of a new system would not be known in advance. And as a result, when such a system is deployed, the engineering team would need to fix them on the plant floor. That typically is a time-consuming and costly effort. And worse, it disrupts the operations of a production system.
In contrast, virtual commissioning of a robotic or a hybrid human-robotic system is done before commissioning of the physical systems and, naturally, before deployment of that system to the production floor.
The intent of this approach is to use a digital twin of the system and examine how it works in a virtual representation of the environment it will be operating in. At a basic level, the work would ensure physical issues do not crop up. For example, an engineering team might see that when a robotic arm swings around, it crosses the path of another moving element of the production line.
Similarly, the programming logic can be examined. They might find that a robotic system would be more efficient if it did a set of tasks in one order versus another.
During these processes, engineers can identify and address issues like programming bugs or mechanical interference. The important point to note is that all of this work can be done without disrupting the working production systems.
Bottom line: virtual commissioning saves time and money, and it avoids interruptions of existing work cells, production lines, and plants.
With such benefits, virtual commissioning is being used to prove out different types of systems. That includes pure robotic systems and hybrid human-robotic systems. But the technology is especially important when there is a need for a special machine to be constructed for an entirely new task.
In all cases, the aim is to get the programming, installation, and operation of the system right the first time. It should operate as planned once it is in place.
Additional Resources
Drive Production Excellence with Intelligent Manufacturing
The automotive industry is facing unprecedented challenges, with rapid change and intense pressure to meet the demands of climate change, regulations, and consumers. Download Now
Modernize automotive factories with Siemens Smart Manufacturing solutions
Discover how automakers can transform their business with Smart Manufacturing solutions using state-of-the-art hardware and software to modernize production lines. Watch Now
Virtual Manufacturing Development for the Automotive Industry
Companies in the automotive industry are pushing to develop the next generation of autonomous, electric, connected, and shared vehicles. View Now