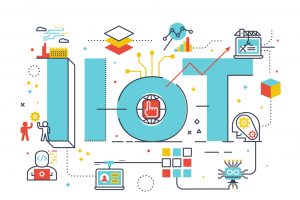
Most manufactures (84%) are currently implementing or evaluating digital manufacturing strategies, whereas only 27% were doing so in 2018.
The Covid crisis may have pushed more organizations into the digital realm, but digitization has been pursued in earnest among manufacturers for the past two years. Initiative including process simulation and the internet of things have been moving forward a an impressive pace.
The growth of digital initiatives among manufacturers was explored in a recent survey of 200 manufacturing executives, which finds industrial IoT adoption is three times higher than it was just two years ago. The survey, jointly conducted by SME, a professional association of manufacturing professionals, and Plataine, an industrial IoT provider, was conducted before the Covid-driven shutdown in the spring of 2020.
See also: Mutually Complementary: Continuous Intelligence, IIoT, and Digital Twins
Just about all respondents, 84%, are currently implementing or evaluating digital manufacturing strategies, whereas only 27% were doing so in 2018. Respondents who participated in the 2020 survey indicated their companies are making strides to become digital. 41% of respondents indicated their companies are at least “mostly digital” in 2020, up from 26% back in 2018.
More than 66% of respondents find Industrial IoT as a very important part of the future of their company’s success. The main technologies that are part of industrial IoT include process and product simulation (76%), big data and analytics (69%), and 3D printing/additive manufacturing (64%). Also seen as key to IIot initiatives are autonomous robots and sensors (56%) and product and plant digital twins (56%).
Survey researchers took a close look at the patterns among digital leaders (27% of respondents), of whom 69% have implemented or are implementing Industry 4.0 solutions, versus 48% of late adopters.
The motivations for moving to digital vary. A majority of advanced manufacturers, 54%, point out that their main challenge is to lower production costs and 51% are looking to improve on-time delivery and estimate delays. Another 47% seek to lower their quality risks. At least 39% seek to improve their ability to predict machine or tool failure.
While the survey has marked progress toward digital manufacturing, there is still much to be done, the SME report’s co-authors report. “While the manufacturing sector generates a great amount of data, only a few companies are harnessing it to improve operational efficiencies,” they state. “In the next decade, digital manufacturing technologies will allow companies to connect physical assets by a ‘digital thread’—unleashing a seamless flow of data across the value chain that will link every phase of the product life cycle, from design, through production to distribution, point of sale, and use.”