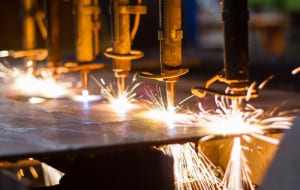
Teel Plastics used an IoT gateway system for one-click manufacturing that optimized production and enabled predictive maintenance of equipment.
Name of Organization: Teel Plastics, Inc.
Industry: Manufacturing
Location: Baraboo, WI USA
Opportunity or Challenge Encountered
Customized manufacturing has been around for some time, with products tuned and configured for all customer needs. Now, Internet of Things (IoT)-based approaches are providing custom manufacturers even more power to reduce human error, gain increased visibility into the granular details of the manufacturing process, and conduct predictive maintenance.
For more than six decades, Teel Plastics has specialized in custom extruded plastic tubing and profiles. Teel Plastics products are used in geothermal pipes, solar film cores, coextruding products, healthcare tubing, film cores, converting cores, filtration components, industrial tubing, and more.
The Teel facility in Baraboo, Wisconsin has 10 manufacturing lines that produce different products at various times throughout the day. Each line requires a custom recipe for every product. These recipes include different material inputs, equipment, heating components, and other variables. Recipes can change several times in one day, and ones that haven’t been used in months can resurface when new orders come in.
All these variables quickly caused instances where human error produced deviations in the recipes. These deviations inspired Teel Plastics to find a solution that would allow operators to control all pieces electronically and reduce human error.
“There are many variables that go into a single recipe, and our employees are interacting with and having to memorize and apply multiple recipes during a single shift,” said Owen Gwynne, senior programmer with Teel Plastics. “There are a lot of different reasons for errors—employees are moving too quickly, it’s a recipe they are unfamiliar with, or they’ve entered in the middle of production—but what seems like a miniscule issue can lead to our products having flaws or manufacturing downtime. We knew there had to be a way to minimize some of this error.”
How This Opportunity or Challenge Was Met:
Recognizing the need for connectivity, data access, and scalability, Teel Plastics executives worked to develop a competitive strategy that would also enable them to capitalize on the benefits of the IoT. They began by identifying the fundamental technology that would fuel their IoT effort.
The goal was to implement a solution capable of speaking to an entire range of PLCs from vendors, including Allen-Bradley and Siemens. To accomplish this, Teel adopted Kepware’s IoT Gateway for KEPServerEX to control all of the essential components on its manufacturing line through a single web interface.
Benefits From This Initiative:
As a result of the implementation of IoT-driven custom manufacturing, Teel Plastics now has real-time data on whether customers’ needs are being met, and has been able to increase its visibility into the granular details of the manufacturing process. The company also is seeing increased product output and quality through more informed decision making and reduced downtime, and has removed the risk of human error in manual tasks. Put simply, the new system has reduced stress and improved ease of mind for operators.
With the Kepware solution, a line operator can send a pre-saved recipe with more than 20 parameters from a web interface to the IoT Gateway, which then distributes the instructions to the machines on the line. This is a much more efficient than the previous manual process, and by providing device connectivity to multiple PLCs including Allen-Bradley and Siemens, Teel drastically reduces risk of human error. With these new processes, Teel reduced its set-up times by 30 percent. In addition, operators no longer have to memorize recipes, which allows them to complete tasks with greater confidence. Additionally, switching between shifts has never been smoother, as incoming operators can easily pick up right where the previous operator left off.
“By incorporating the IoT throughout our shop floor, we’ve been able to take something that previously required memorization and 30 to 40 clicks and bring it down to a single click of a button,” Gwynne said.
With increased visibility into the granular details of its manufacturing process, Teel has in-depth plant floor data enables its engineers to test different variables, which has led to decreased downtime. By monitoring different aspects of production (such as room temperature) and making slight adjustments, Teel Plastics has also made its recipes much more efficient. In addition, aggregating data on indicators (such as humidity or wear on parts) into a central database enables operators to monitor equipment for predictive maintenance, and leadership to make more informed decisions on recipes—so the company can produce greater output at a much higher quality. For example, prior to the IoT Gateway implementation, one line was completing 18 units a minute. Now, it is outputting 35 units a minute—nearly doubling its capacity.
Finally, Teel Plastics customers can now see detailed data that proves their requests are being met to their exact specifications. This visibility has increased customers’ comfort with standard requests and has even led many to expand their requests.
(Source: Kepware)
Related: