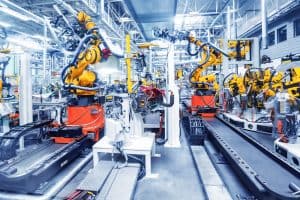
Manufacturers will turn to smart factories and offices, allowing critical functions to be monitored remotely or, at a minimum, by fewer people.
While many manufacturers had been exploring or experimenting with technology approaches to automating their production lines and supply chains in recent years, the Covid-19 crisis pushed things ahead by at least five years. Such has been the case with artificial intelligence and machine learning, which saw a rapid acceleration in adoption during 2020.
For one, there have been shifts in consumer behavior that demanded — and continue to demand — greater automation and virtualization, according to a report in Manufacturing Global. “We will see advancements in how IoT and augmented and virtual reality better enable the non-remote workforce,” according to Rajaram Radhakrishnan, senior VP at Cognizant. “Smart factories and offices will increase, allowing critical functions that currently need to be overseen in person to be monitored remotely or, at a minimum, by fewer people.”
A recent survey of 1,000 senior manufacturing executives from Google Cloud, conducted by The Harris Poll, confirms that the Covid-19 crisis may have spurred a significant increase in the use of AI and other digital enablers among manufacturers. More than three-quarters of executives, 76%, have turned to next-generation technologies such as data and analytics, cloud, and 66% of manufacturers who use AI in their day-to-day operations report that their reliance on AI is increasing.
There are many ways in which AI is being applied. For example, it is instrumental in the “visual inspection of finished products,” the study’s authors report. “Using AI vision, production line workers spend less time on repetitive product inspections. They can instead focus on more complex tasks, such as root-cause analysis.”
See also: Can Factory Work go Remote? Real-Time Information is the Key
Connected factories and AI
Another example of AI in action across manufacturing spaces is powering connected factories to assisting with predictive maintenance. “Custom ML models can predict machine events that left unchecked, could cause unscheduled downtime and negatively impact production schedules,” the report states. “In construction, AI can help builders reduce critical errors that lead to delays while optimizing energy consumption and supporting complex logistics and scheduling tasks.” AI and machine learning (ML) can augment manufacturing employees’ efforts, “by providing prescriptive analytics like real-time guidance and training, flagging safety hazards, and detecting potential defects on the assembly line.”
At this point, almost two-thirds of manufacturers (64%) rely on AI to assist in day-to-day operations, with a quarter already allocating half or more of their overall IT spend towards AI. The average manufacturer now spemds 36% of its IT budget on AI-related initiatives. Among manufacturers who use AI in day-to-day operations, the top three
reasons are to assist with business continuity (38%), help employees increase efficiency (38%), and help employees overall (34%).
The top five areas where AI is currently deployed in day-to-day operations include quality inspection (39%), supply chain management (36%), risk management (36%), product and/or production line quality checks (35%), and inventory management (34%).