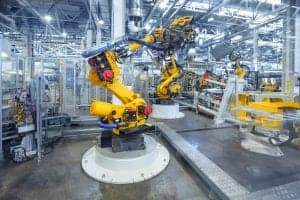
Automation may allow manufacturers to enable remote work and lights-out factories, saving the highest value tasks for onsite production employees.
Over the past year, as the Covid crisis raged, we learned it’s possible to run an information-intensive, office-based company remotely with a work-from-home workforce. But is it possible to also run a factory with a remote workforce?
New data out of Accenture confirms that there is little productivity loss with remote workforces overall. Done right, a hybrid workforce even can increase output. Organizations that enable a resilient workforce to be more productive and healthier anywhere are also reaping financial benefits, the study shows. “A majority of high-revenue-growth companies, 63%, have already enabled productivity anywhere workforce models, where employees have the option of working remotely or on-site. While the vast majority (69%) of negative or no-growth companies are still focused on where people are going to physically work, favoring all on-site or remote rather than enabling hybrid.”
While moving to remote work for office-based or professional tasks has been a relatively straightforward initiative, enabling remote work in manufacturing is fraught with issues. “The physical nature of the manufacturing industry has made the switch to remote work a challenge,” writes Graham Immerman, VP of MachineMetrics, in a recent report published by World Economic Forum. “in April of 2020 just 41% of manufacturing employees were able to telework according to the US Bureau of Labor Statistics. Just 46% of the industry has enabled remote monitoring processes to ensure visibility of production when not at the plant.”
At first blush, it wouldn’t seem to make sense to physically remove many of the workers overseeing assembly or shipment of products from the scene. However, with today’s digital connections, analytics, and robotics, it’s entirely possible workers and their managers could manage automated production and assembly from remote locations, perhaps even opening up possibilities for managing multiple facilities across the globe. “As manufacturers progress in their data maturity and remote work compatibility, they will be able to enable lights-out factories driven by automation, saving the highest value tasks for onsite production employees,” says Immerman.
Immerman makes the following recommendations for moving industrial workforces to remote work:
Monitor the status of production. A challenge with remote work is “if you remove the manager from the shop floor, they have little to no insight into the status of production,” Immerman cautions. “To make the shift to remotely monitor production, machine and operator data needs to be collected and contextualized in real-time, so managers can get insights on production no matter their location.”
Assess the availability and timeliness of data: “The virtual shift will work only if the infrastructure for data collection, analytics, and remote collaboration tools is up to par.”
Analyze the health of equipment. Predictive analytics can play a key role in helping remote teams to maintain machine uptime. “Enabling your equipment providers and service teams with machine condition data helps to diagnose and resolve machine issues faster, before they happen, or even remotely,” says Immerman. “With real-time machine data, manufacturers gain insight into equipment health and conditions to get early warning signs of potential equipment failures and elevated risk areas that lead to downtimes.”
Collaborate in real-time and provide autonomy to onsite workers. “Remote work highlights the importance of real-time, automated communication and notifications to ensure the right information is in the hands of the right person at the right time,” says Immerman. “This means leveraging real-time production data to drive automated notifications, or predictively alerting a maintenance supervisor of an impending machine tool failure and automatically generating the work order in a computerized maintenance management system (CMMS).”
Upgrade digital skillsets: Managers need to assess who must still work inside the factory, and who can perform the same tasks remotely. “Whether it’s reliability, quality, engineering, or other subject-matter experts, the specialized focus of their work makes it more conducive to performing digitally. Having these professionals offsite also lets them remotely serve multiple factories and cross-pollinate across the enterprise.”