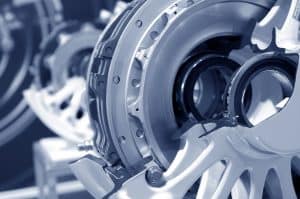
Argonne National Laboratory, in collaboration with leading manufacturers, is deploying its machine learning expertise to help with aircraft manufacturing.
The U.S. Department of Energy and Argonne National Laboratory are utilizing their machine learning expertise to speed up aircraft manufacturing improvements, by reducing the amount of costly experiments and simulations.
In partnership with GE Research, EWI, and GKN Aerospace, Argonne National Laboratory is specifically focusing on the welding process and running detailed simulations with input from three of the industry’s largest manufacturers.
SEE ALSO: Extracting Data from Aerial and Satellite Imagery Using AI
The machine learning algorithm, developed by an Argonne National Laboratory team led by computational scientist Prasanna Balaprakash, is a scalable machine learning package which trains itself to find the best solution to a query.
“If you’re trying to brew the best cup of coffee, you can spend several hours fiddling with the many settings on the best machines,” Balaprakash said. “In trying to make airplane parts, we can avoid this by using machine learning, which gives us the ability to learn from a handful of example settings and identify the best one from a set of a billion possible configurations.”
Instead of human trial and error, the machine learning program is able to run millions of simulations with minuet changes to the variables. It is fed a dataset of welding conditions and parameters, and will then analyze and rank each variable to find the best welding process for aircraft manufacturing.
“Manufacturing airplane parts involves highly complex, sophisticated and expensive machines, and automating their manufacturing can save money and time, and improve safety and efficiency,” Balaprakash said.
The funding is provided by the Department of Energy’s Advanced Manufacturing Office and the three collaborators are able to use Argonne’s supercomputer facilities to test welding processes.