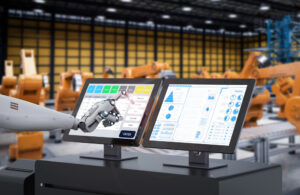
Factory managers need reliable data to drive real-time analytics and AI-driven insights of their manufacturing operations.
Manufacturing may be considered one of the final frontiers in the real-time world. These are capital and resource-intensive businesses in which even approaches such as the internet of things, just-in-time, and automated factories have a large degree of latency across product delivery flows. Artificial intelligence change that, but a large number of factory managers aren’t aboard with AI yet.
By 2040, factories will rely almost completely on AI-enabled self-learning machines and robots, overseen and assisted by human workers, a recent survey of factory managers by Accenture predicts.
A sizeable number (62%) of managers consider AI as a key enabler for all aspects of
factory operations, the survey shows.
In the near term, however, most are prioritizing maintenance, repair and overhaul (MRO) processes, logistics optimization and production efficiencies. This is where AI can have a significant impact, the Accenture authors state. “AI-powered predictive maintenance can eliminate machine defects before they occur, optimize MRO scheduling to minimize production disruptions and extend the lifespan of equipment.”
See also: Smart Factory Changes Afoot in 2025
Transitioning from forecast-based production planning to demand-driven manufacturing “will be crucial for factories to adapt dynamically to demand fluctuations, supply-chain disruptions, and operational constraints,” the co-authors state. More than half of respondents said they believe “demand-driven manufacturing will replace traditional, forecast-based production planning. The transition to dynamic, event-driven systems that can continuously optimize operations will be a boon.”
AI-driven logistics solutions “can help manufacturers anticipate demand fluctuations, prevent
supply chain disruptions and optimize inventory management,” they add..
There is a wide array of initiatives tied to AI coming down the pike, they add. Approximately half of the respondents stated that, by 2040, hyper-automated factories will rely on the following key elements:
- Autonomous operations (53%)
- Self-learning machines using generative AI (52%)
- Completely automated warehouses (51%)
- Smart connected manufacturing cells (49%)
- Autonomous mobile robots (AMR) (49%)
- Digitally connected crews (48%)
- Digital operations twins (47%)
- Automated guided vehicles (AGV) (45%)
AI will be employed to “link machines autonomously and prioritize tasks to distribute workloads and create optimal work sequences,” they state. “The factory operation´s predictive analytics-based processes will monitor sensor and visual data, thereby automating maintenance schedules and quality checks by pre-emptively detecting and forecasting equipment malfunctions and product defects.”
At the same time, 38% of factory managers are still hesitant about applying gen AI in their factories. “Lingering mistrust and the need for more awareness about how effective this technology can be in manufacturing are a few of the reasons,” the authors state. “But poor and inconsistent data quality is the main cause. Factory managers need reliable data to drive real-time analytics and AI-driven insights.”
To build the factory of 2040, “factory managers need to focus on data now,” they add.