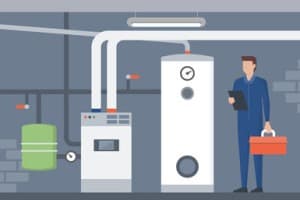
“Imagine being able to send the right technician with the right parts every time.”
Name of Organization: Hamilton Engineering
Industry: Water heating systems
Location: Livonia, MI USA
Business Opportunity or Challenge Encountered:
Hamilton Engineering, a maker of custom water heating systems for commercial and industrial customers, wanted to let its technicians monitor and control installations at customer sites.
The company has been manufacturing commercial/light industrial high-efficiency condensing water heaters and heating boilers for more than 15 years. Three years ago, Hamilton launched its 3VO line of condensing boilers and water heaters. The line features a fully serviceable heat exchanger, and new controls that allow the appliance to automatically adjust to changing conditions, wear and fouling, as well as keep users informed of that wear and the impending need for service.
As documented in a recent case study, the company needed true two-way communication and real-time operating data — including wear and fouling – for its high-efficiency commercial/industrial heating equipment. Hamilton wanted access control that allowed the same monitoring system to be shared by engineers, distribution partners, customers, and service technicians.
How This Business Opportunity or Challenge Was Met:
Hamilton worked with B-Scada to build a monitoring system to provide visualization for real time and historical data, as well as reporting, alarming, analytics, workflow and mobile device access.
Within the system, data is routed from the boilers by Hamilton engineers through Advantech’s Wzzard cellular gateway over a secure, private cellular network provided by Verizon, and then to B-Scada’s Status Device Cloud IoT platform.
The B-Scada solution provides access to real-time system data anywhere, at any time, to authorized users on any device. The system includes real-time two-way communication, trends, alarms, and notifications. The solution also provides four different security levels, ensuring that users of different access levels are able to access the information they need to do their jobs. This enables the same system to provide actionable information to managers, distributors, engineers, operators, and maintenance technicians.
Measurable/Quantifiable and “Soft” Benefits From This Initiative:
One of the most-appreciated features of the new B-Scada system is a dashboard information presentation that provides notifications related to specific events. When end users ask Hamilton’s service technicians to look into their water heating systems, the technicians can look at the system from a computer or device for component-specific and site-specific troubleshooting.
“Imagine being able to send the right technician with the right parts every time; not wasting the time or money to do a preliminary visit to determine the problem and solution, and not sending a highly qualified and expensive technician when an entry level technician could do the work properly,” said Jeff Deal, CEO of Hamilton Engineering, quoted in the case study. The system also allows service companies “to do much of their work remotely; from their desktop instead of from a fleet of service trucks and service people. It further allows both distributor level and factory level technical support without having to visit the jobsite.”
Hamilton Engineering also is saving a significant number of service technician hours, especially since they may have installations that can be six to eight hours driving time away. “This system will alleviate much of the time and manpower lost trying to service those remote systems,” Deal said.
(Source: B-Scada)