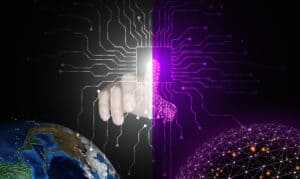
Digital twins help organizations understand and put into context the massive amounts of data available in autonomous factories.
Some call it the “Industrial Metaverse.” But before we make too much of this term, especially as it relates to the Industry 4.0 space, let’s look at what’s at the core — digital twins. The key to digital twinning in industrial settings is the fact that it makes operations and configurations easy to see to simulate changes or act of problems.
With an increasing movement toward enabling an almost fully autonomous factory, interconnected with Industry 4.0 capabilities, companies face a need to process and contextualize massive amounts of data, according to an eBook published by Visionaize. “With mountains of data as the necessary fuel to make the autonomous factory run, it’s essential this data be organized and presented in an intuitive way so that humans can quickly understand, plan, and simulate each step of the journey before it’s put into production,” the book’s authors state. “Furthermore, the data visualizations that are intuitive for the business analyst, using increasingly sophisticated cloud and analytics technologies, are vastly different from what will allow the operations worker to make practical use of the data to take action on the shop floor, within the refinery, construction site and other operational settings.”
See also: Digital Twins, IT/OT Convergence Drive the Industrial Internet
Digital twins provide a framework to address this challenge, but maintaining the 3D model to be a precise replica of the actual physical plant is critical. To start and build a digital twin within a production facility, the book’s authors make the following recommendations:
Lay the foundation: “The starting point for 3D digital twin models can be created in two main
ways — importing CAD engineering models, or incorporating visual data from across facilities. “Import and use 3D CAD engineering models, and then update the 3D digital twin model to reflect real-world variances and changes,” the book’s authors advise. Or when 3D CAD models are not available, “various methods using laser scanners, LIDAR and drones can capture the visual data necessary to create the model foundation.” All these elements can be integrated into a complete, and coherent visual
foundation for the digital twin.
“Intelligize” the twin: Once the foundation is established, employ AI-powered processes to intelligize the model, the report’s authors recommend. “Using the information from asset master systems, highly precise attach points called tags are created, and accurate asset, process, and other attribute labeling is added. These tags become the conduit through which relevant data can flow, providing a highly intelligent, spatially aware model. They are also the integration points for data tools, including data and AI platforms.”
Connect the twin: Next, expose and attach the model to data sources, either by connecting directly to enterprise systems or data and analytics platforms, the authors state. The connections to enterprise systems can be made “through API’s and connectors. These near-real-time connections can be bi-directional, with the ability to write-back to systems of record.” Data and analytics platforms that can feed digital twin presentations may include data warehouses, data lakes, AI and machine learning platforms. “These connections allow the 3D twin to display highly intelligent AI-generated insights, predictions, and
recommended actions.”
Maintain the twin: Employ change management that enables the model to be updated as changes are made in the physical world without taking the model offline, the report’s authors recommend. This allows operators and other end-users continuous access to the tool on a 24/7/365 basis. “This is accomplished by a combination of software functionality, business processes, and visual data capture required to update the 3D digital twin.”