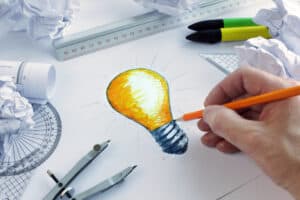
We’re at the confluence of the use of three industry technologies – high-performance computing (HPC), simulation, and data analytics – that will change the way businesses operate and products are designed, updated, and supported.
The convergence of high-performance computing (HPC), simulation, and data analytics is poised to change how products are designed, updated, and supported. The use of the technologies will also change the relationship between the manufacturer and the customer.
In the future, it will no longer be a one-time engagement where the vendor sells a product and moves on. Instead, there is the potential for a constant interactive connection between the vendor and the product in the field, as well as the vendor and the customer, where the analysis of the data from such feedback loops can be used to refine and improve the product’s design, prevent failures and downtime, ensure the product is operating optimally in the field, and enable new business models.
Marrying Design, Simulation, and HPC
Most designers use computer-aided engineering (CAE) or computer-aided design (CAD) tools to create new products that are lighter, stronger, longer-lasting, and better performing. With simulation tools, they can see how the product performs in a virtual environment under various conditions.
Let’s first look at what’s happening with design. CAE and CAD have always been used to reduce prototyping and physical testing, both of which can be costly and time-consuming. The availability of the latest generation of HPC resources for both on-premises or cloud CAE and CAD lets companies run iterations faster and faster, fine-tuning design at each step.
Similar benefits are achievable for simulations. Increased HPC capabilities have allowed much more granular and realistic simulations. In both arenas, HPC applied to design and simulations can eliminate the need for prototyping altogether.
Enter the Connected Product
After a product is sold, product engineers typically get very little feedback about its performance in the field. That no longer has to be the case. Many products, both industrial and consumer, incorporate sensors and IoT devices and constantly share the data from these devices with the manufacturer.
Companies can use that data about the product and gain great insights into its performance while operating in the field. Analysis of this data can help identify problems in the making or spot analogies that require additional attention. The availability and analysis of this data is often used by manufacturers and service organizations to implement predictive maintenance (sometimes called condition-based maintenance) efforts.
But there is even more use for this data. Product manufacturers can combine system simulations and IoT data to improve product designs using simulations based on real load cases.
See also: Digital Twins May Soon Make Crash-Test Dummies Obsolete
Data Analytics, AI, and Digital Twins
Taking this approach to a higher level, a manufacturer could run many simulations to create “synthetic” data and then combine this with sensor data on how that product performs in the real world to get deeper insights into its operations.
In particular, some manufacturers are applying advanced analytics, machine learning, and artificial intelligence to explore the vast amounts of synthetic and real-world data to help make smarter decisions about their products faster.
For many, the work in this area is focused on digital twins. Digital twins are being built through the convergence of simulation technology, high-performance computing, and artificial intelligence. Digital twin technology can make use of data streams to create a digital representation of a real-world asset.
Some call this area of work analytics-based product engineering. It lets manufacturers take live performance data from a product in the field and push it back into the product simulation model to improve the product design. With the live production data being fed back into the model, a closed-loop digital twin is created.
The technology’s potential is significant. Product and facility testing involving physical objects could soon be rendered unnecessary. That’s the takeaway from a survey of 2,007 business and IT executives published by Altair, which foresees an end to physical prototyping in the next three to six years, as projected by 67% of respondents.
Organizations are using digital twin technology for a wide range of functions and reasons. For example, 95% are using them to better inform new product development, 51% to create smart objects, and 50% to monitor real-world objects in real time.
Making Use of the Digital Twin Feedback Loop
One example of making use of this real-time data feedback loop is that manufacturers can better understand how their products are being used in the field. A product may have been designed to operate at a certain performance level or temperature. But the data from a working product analyzed in a digital twin might show that it can safely operate outside that range.
Additionally, when manufacturers have access to vast amounts of operational data about the units in the field, that data can be fed back to the R&D department to see if there are things that can be changed in future iterations of the product.
The data might find overheating under certain conditions. The product group might use that data to perhaps add a fan or a vent to the design. Or the data might reveal that many customers have trouble operating the equipment. That information might be used to simplify operations, make things more intuitive, or provide visual clues on a console.
A Final Word
The convergence of model-based simulation and data-driven simulation solutions powered by HPC has the potential to improve design efficiency, enable predictive maintenance, and optimize the use of products in the field.
These trends and the application of these technologies have a far greater impact beyond engineering and product manufacturing. The same techniques and technologies are now finding applications across all industries.