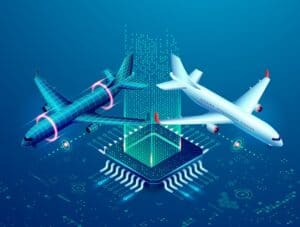
Digital twins can revolutionize and rapidly speed up the product development process, reducing the time to market. They also allow for rapid iterations and optimizations of product designs far faster than physically testing every single prototype.
Digital twins have been seen as a technical construct, but they are much more about advancing the business. Less waste, shorter times to market, constant customer insights: the advantages of applying digital twins are many—if you get the conditions right.
That’s the word from a recent panel discussion out of McKinsey, in which Kimberly Borden and Anna Herlt, both with McKinsey, made a compelling business case for digital twins. “There is a tremendous amount of value a digital twin can bring,” says Borden. “One of the biggest areas of value is reducing time to market, development time. It allows for rapid iterations and optimizations of product designs far faster than physically testing every single prototype.”
A digital twin can revolutionize and rapidly speed up the product development process, Herlt agrees. “It can either help you to reduce the material in your design, so overall material consumption, or you can improve the traceability of the product to reduce quality issues and, ultimately, also reduce waste for our environment.” Consumer electronics manufacturers have been employing digital twins, resulting in a 20% reduction in scrap, she adds.
See also: Report: Demand for Digital Twins Growing
Product quality may be the killer application for digital twin technology, bringing “tremendous improvements” in the manufacturing process, Borden adds. “After you simulate the product in manufacturing, it’ll allow you to see where there are flaws in the design in order to better manufacture it. Further, in service, you can actually see how the design may not be functioning appropriately, and therefore you can redesign it in real time.”
There are also potential increases in revenue “of as much as 10 percent by developing customer twins that allow customers to fully interact and immerse themselves within the product,” she continues. A compelling example of this is enabling customers to test drive automobiles virtually.
Of course, high-functioning digital twins aren’t built overnight. “One of the key things you need in place is a strong data infrastructure,” says Borden. In addition, it takes certain skills to build and support a digital twin environment, especially if the twin is sophisticated. Other challenges are “the large up-front investment that is required before you really can get to the full value, and then the lack of access to the high-quality data that the twin would actually require,” Herlt adds. “Many companies need to identify where to start—that is, which is the most relevant use case to start with. We typically try to pick one that is not too complex and actually build out the entire digital-twin framework from there.”
Borden outlines the three essential ingredients needed to make digital twins work:
- Data engineering and data science resources “to support that data infrastructure and put the twin together.”
- Physical-modeling capabilities “to model the product or the facility that you’re trying to twin.”
- For more complex situations, “advanced simulation and analytics skills in order to speed the compute power.”
“If you are trying to twin a fighter jet, for example, that takes a tremendous amount more computing power than twinning a toothbrush,” says Borden. “Overall, a higher level of digital maturity will make it easier for implementation.”