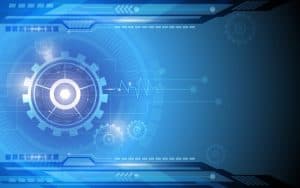
As AI in manufacturing changes how machine health is monitored and managed, companies will need machine ops specialists to bridge the gap between operations and maintenance.
AI in manufacturing can enable the digital transformation of the industry into a more effective, skillful, and productive version of itself. It can help enhance record-keeping, inventory management, and supply chain flow. Through machine data analysis, it can also significantly improve machine health. AI can diagnose existing problems and provide predictive insights to save manufacturers time and money on maintenance and repairs.
AI’s greatest gift might be the time it gives back to employees. With AI managing more repetitive or mundane tasks, frontline workers, technicians, and managers are free to focus on strategic tasks that yield more value. But for this gift to be realized, employees have to know how to work with AI and make it work for them.
This is where the challenge comes in. The introduction of AI and automation to the industry has highlighted skills gaps that can hinder the progress of digital transformation in manufacturing. Workers need the right skills to work with AI and its developers to create practical AI use cases in manufacturing. Without this, manufacturers will never be able to harness the true power of AI to inform intelligent and efficient decision-making.
Skills gaps exist throughout the industry, from frontline workers to managers. To create a future where AI and skilled workers operate in sync, manufacturers must address these gaps now.
See also: 4 Ways Industrial AI Will Reshape Manufacturing in 2022
Factory floor workers and technicians
One area where AI can bring the most value is machine health. Technology can provide real-time data on the condition of machinery and offer deep insights that make it possible to go beyond reactive and preventive approaches into the realm of predictive maintenance. AI-enabled machine health monitoring significantly reduces downtime and can accelerate a manufacturer’s digital transformation efforts. However, that’s assuming those working on the factory floor are ready and able to take advantage of its potential.
Technological innovation in manufacturing should not replace frontline technicians. Instead, it should make their jobs more efficient and should free up their time for higher-value work. Unfortunately, this is not always clear to the people who have been doing their jobs for years without the help of AI. To move the conversation forward and address skills gaps, manufacturing leaders must address why workers would want to learn the skills necessary for implementing AI in the first place.
Show employees how AI in manufacturing can take over day-to-day tasks, freeing them up to take on more profitable work that requires innovative thinking and problem-solving skills. Once you’ve done that, you can begin equipping workers with the right skills to realize the value potential of AI.
Chief among these skills is data-informed decision-making. To meet the future of manufacturing head-on, maintenance teams must understand the data they’re given and act on it. That doesn’t mean everyone has to become a data scientist overnight — machine data from AI can be presented in a digestible way — but interpreting that data will be an important skill to learn.
Maintenance teams and technicians must also learn to collaborate with one another and with other stakeholders to take advantage of the insights machine health monitoring provides. For example, if the AI is telling technicians that a bearing will break in the near future, they should know to reach out to inventory management to ensure the parts they need will be there when it comes time to fix it.
Machine health monitoring also makes it possible for maintenance personnel to be more precise than ever before. Incremental improvements that might have once gone unnoticed can now be fully realized, assuming people know where to look. That might mean, for example, switching to a more secure thread locker when worn bearings start to cause more vibrations. AI-enabled tools might sense and report the vibrations, but it’s up to people to know what to do with that information.
The bottom line is that digital transformation in manufacturing is not meant to turn AI into the star of the show. Instead, AI-enabled tools should act as supporting players, enabling frontline workers to elevate the value of their work. For this to be possible, employees must understand how their roles will evolve and how they can take advantage of the power of AI to improve their decision-making and efficiency for the future.
See also: 6 Rules for Energizing the Data Behind Industrial AI
Manufacturing management
The value and impact of AI can extend beyond factory floor workers and technicians as well. In fact, digital transformation in manufacturing can only be successful if managers are equipped to manage the changes taking place within the industry. Everything — from the pandemic to climate change to supply shortages to technological innovations — plays a role in shaping how manufacturing will look for years to come. To successfully navigate all of this, managers will need to get comfortable challenging the status quo and driving innovation.
That means being ready to experiment. Manufacturing leaders might not have acknowledged and rewarded experimentation as a prized manufacturing skill in the past but trying new things and learning from failure and success will be a crucial part of agility and adaptability. This mindset shouldn’t be limited to product development — experimentation can be applied throughout the organization.
For example, with AI in manufacturing freeing up more time for technicians and maintenance teams, it’s up to management to experiment with the best way for employees to spend newfound time. On the technical side, workers can use AI-enabled machine health data insights to try out different ways to reduce operational costs and make inventory management more efficient.
A willingness to buck the status quo also extends to the hierarchy of the business itself. The traditional structure that separates factory floor workers from management will hinder digital transformation in manufacturing. Instead, managers need to create an agile structure that can adapt to handle new challenges.
Part of this involves finding the people within the company also willing to drive change and challenge the status quo. The employees who experiment and seek innovation and improvement will be the ones who help push the business forward. Traditionally, leaders might have seen this type of employee as more of a hindrance than a help. It’s time for that attitude to change.
Managers can’t afford to view themselves as above the changes happening within the company and the industry as a whole. They’re an integral part of digital transformation in manufacturing, and they must be willing and able to adapt — and to help others do the same.
The emerging roles of digital transformation
In addition to the new skills needed among both frontline workers and managers, there will also be emerging hybrid roles due to new challenges and opportunities of digital transformation in manufacturing. These positions will straddle the divide that traditionally exists between management and frontline workers and blur the lines between traditional areas of expertise to drive new value, innovation, and growth.
For example, as AI in manufacturing changes how machine health is monitored and managed, companies will need machine ops specialists to bridge the gap between operations and maintenance. These teams will drive an AI-enabled predictive approach.
Technology also enables maintenance teams to share precise and predictive data with anyone, anywhere in the world. This means off-site experts can easily lend their expertise to help solve specific problems through video. Remote collaboration might not have been a priority in manufacturing before, but it has a role to play in digital transformation today, and companies will need virtual shift champions to help workers and managers adapt.
What’s more, as employees are tasked with challenging the norm and driving innovation, they’re likely to feel the culture of their organizations shifting. This is where a new role of cultural translators can help encourage employees to lean into the changes and adapt alongside them to drive more value.
Traditional manufacturing roles are changing, and new positions are emerging. It’s an exciting time as manufacturing transforms into a more digital and dynamic industry. But it will be up to manufacturing leaders to ensure their organizations keep up. Give teams the skills they need to take full advantage of AI in manufacturing today and adapt to the needs of the future.