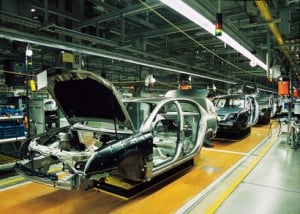
Cyber-physical systems are changing today’s manufacturing practices by bringing the physical environment where goods are produced closer to the cyber environment where the production is orchestrated. As RT Insights contributor Dr. Darko Anicic explains here, these systems leverage event processing as a critical technology which enables real-time information to flow from the physical environment to the cyber environment and vice versa.
Over the past three centuries, many new manufacturing technologies have been developed, all aimed at making production faster and more efficient. New technologies continue to arise such as nanotechnology, genetically engineered crops, 3-D printing, new types of composite materials, and sophisticated robots to automate assembly lines. In manufacturing, the introduction of new computer technologies makes it easier to customize products and ensure just-in-time (JIT) production. One such advancement is the cyber-physical system (CPS).
A CPS interacts with both the real, physical environment and a virtual, digital environment. It gets information from the physical world, processes it in the cyber world, and utilizes results to impact the physical world. Unlike traditional embedded systems, a CPS typically consists of networked devices which interact. CPSes are used almost everywhere such as in health care, aerospace and avionics, transportation and automotive networks, energy optimization systems, efficient agriculture and environmental science, disaster response systems and personal fitness systems.
CPS technology is still emerging but the possibilities of their use in automated production systems are endless. For instance, a product can be instructed to navigate itself throughout a production workow. At each stage of the workow, the product can give commands to machines, complain if a part has been wrongly installed or instruct a logistics service on how to transport it.
What Event Processing Is
Event processing (EP) is seen as one of the key technologies that enable the use of CPSes in modern manufacturing. EP provides concepts and techniques to process real-time data generated by CPSes and to make sense out of it. If CPSes can be seen as infrastructure which enable interplay between a physical and a virtual environment, then EP can be seen as a main building block of this infrastructure.
For instance, by processing events from custom environments and field production devices, the overall ongoing production can be adapted on-the-fly. Similarly, by processing events from CPSes related to energy consumption and carbon emissions, we will get an accurate forecast that goes way beyond traditional ones. Consequently, it will enable short-term production planning as opposed to traditional, long-term forecast models and, ultimately, will provide JIT production.
Thanks to CPSes, the border between the digital and the real world is disappearing. Physical devices at the production floor can be effectively monitored and controlled with intelligent networking. Internet-connected production systems can also communicate across corporate boundaries in order to react quickly to changes.
However, these intelligent, networked CPSes only provide the basic infrastructure for optimized production. To achieve the most efficient manufacturing processes, the next step will be to enable even smarter CPSes which can act autonomously at the production floor level, yet be able to fulfill goals established at a higher, production-planning level.
EP will certainly contribute to making manufacturing more efficient and, hopefully, to expanding the quality and quantity of production. The emergence of CPSes and EP represents another major step forward in manufacturing technologies.